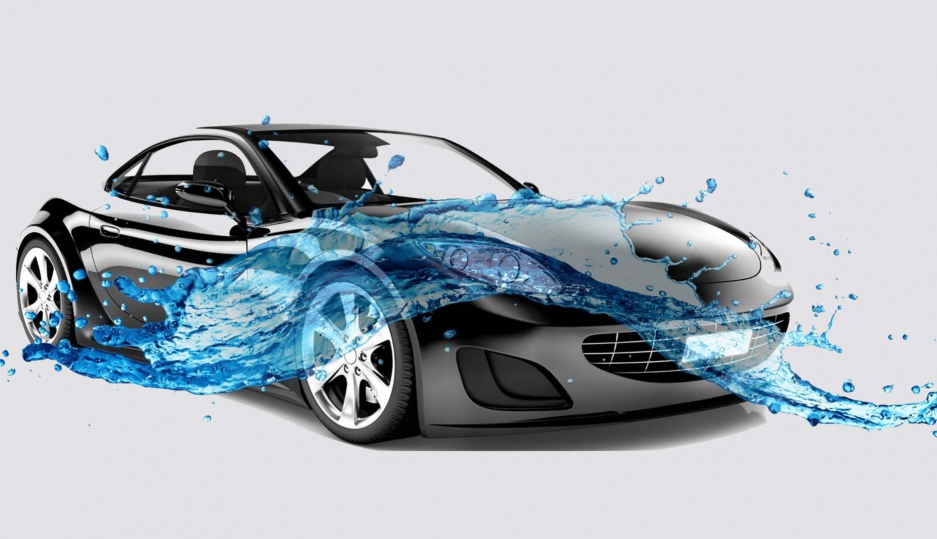
Tudo sobre e-coat: as características, a química de eletrodeposição envolvida durante a pintura e os diferentes tipos disponíveis no mercado
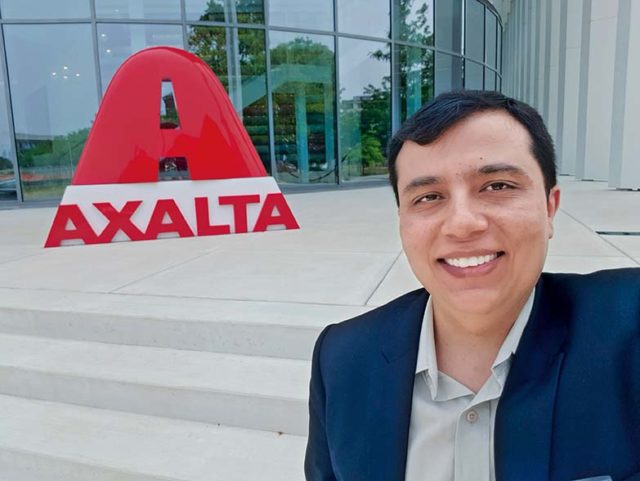
Allan Cezar Vieira dos Santos
É integrante do grupo de Pesquisa e Desenvolvimento em tintas automotivas da Axalta Coating Systems do Brasil e atualmente supervisiona o Laboratório de Tintas E-Coat da unidade de Guarulhos (SP).
Abstract
The electrodeposition coating (e-coat) may be defined as an immersion primer, which is applied under the action of electrical current. This paper presents a brief technical introduction to this material, considering its general features, the electrodeposition chemistry involved during the coating process and the distinct classes of e-coats available at the market.
Resumo
A tinta de eletrodeposição (e-coat) pode ser definida como um fundo (primer) de imersão, o qual é aplicado sob a ação de uma corrente elétrica. Este artigo apresenta uma breve introdução técnica a esse material, considerando suas características gerais, a química de eletrodeposição envolvida durante a pintura e os diferentes tipos de e-coats disponíveis no mercado.
A tinta para pintura por eletrodeposição é conhecida comumente pelo termo e-coat, apesar de outros nomes também fazerem parte de nosso cotidiano, tais como KTL (do alemão Kathodische Tauchlackierung), Elpo ou ED.
Ela representa uma tecnologia à base de água para utilização exclusivamente industrial e aplicável a superfícies condutoras de eletricidade; nesse cenário, substratos ferrosos equivalem à maioria dos objetos de interesse.
O e-coat pode ser definido como um fundo (primer) de imersão, o qual é aplicado sob a ação de uma corrente elétrica. Em sua formulação, a tinta emprega resinas com grupamentos químicos terminais que, sob indução elétrica, apresentarão carga elétrica positiva ou negativa, sendo atraídas pelo substrato a ser pintado e que deverá apresentar carga elétrica oposta à da tinta.
Esperam-se, portanto, dois tipos de e-coats, a saber:
- E-coats anódicos: no qual a resina apresenta grupamentos químicos de carga negativa e será atraída por um substrato com carga positiva – o ânodo do sistema.
- E-coats catódicos: no qual a resina apresenta grupamentos químicos de carga positiva e será atraída por um substrato com carga negativa – o cátodo do sistema.
Como vantagens frente a outras tecnologias de pintura, podemos citar:
- Automação completa do processo de pintura, permitindo que uma unidade produtiva atinja o conceito de ‘Indústria 4.0’. O nível de automação atual, por si só, já reduz significativamente o fator de erro humano;
- Espessura uniforme do filme em toda extensão aplicada;
- Confere camada protetora em áreas de difícil acesso, protegendo contra a corrosão, graças a uma característica denominada poder de penetração (ou ‘TP’, do inglês throwpower). Em outras palavras, a tinta é virtualmente capaz de pintar qualquer região da peça que entre em contato direto com o banho;
- Introdução dos módulos de ultrafiltração, o que eleva o nível de aproveitamento da tinta para mais de 98%;
- Resistência à corrosão aos substratos pintados;
- Baixa geração de resíduos finais, além de baixo nível de ‘Compostos Orgânicos Voláteis’ ou VOC (do inglês Volatile Organic Compounds);
- Alto nível de segurança operacional, baixo risco de fogo e explosão;
- Grande velocidade produtiva.
Apesar dessas características, há também algumas desvantagens, que podemos citar:
- Alto investimento inicial em equipamentos;
- Limitação no número de cores, resumindo-se a preto ou cinza para sistemas epóxi;
- Necessidade de controle analítico constante.
Histórico e tipos
O primeiro uso da eletrodeposição para a aplicação de um revestimento orgânico sobre uma superfície metálica aconteceu na década de 1930. O processo era utilizado para aplicar uma emulsão orgânica (látex) em embalagens para alimentos (latas de ferro). Nessa versão, conhecida como ‘coil coating’, o revestimento era aplicado na lâmina do metal antes de sua conformação final como embalagem.
A indústria automotiva iniciou a introdução e a comercialização dessa tecnologia na década de 1960, motivada pelos seguintes fatores:
- Segurança: os tanques de pintura por imersão base solvente eram perigosos (risco de incêndio);
- Ambiental/Ocupacional: a pintura por imersão com tintas base solvente apresentava grande emissão de compostos orgânicos voláteis, comprometendo o meio ambiente e, sobretudo, a saúde dos profissionais que trabalhavam nas adjacências do tanque;
- Qualidade: o sistema de imersão vigente gerava carrocerias com grande variação de camada, além de pontos de fervura/escorrimentos.
Originalmente anódicos, os e-coats prevaleceram até 1977, quando começaram a ser substituídos pelos materiais catódicos na indústria automotiva. Há três razões principais para a troca, a saber: a) melhoria na proteção à corrosão através de uma química de resinas aprimorada; b) passivação dos substratos, em vez de dissolução, durante o processo de deposição; e c) um processo mais robusto através da introdução de uma tinta bicomponente para reposição da tinta no banho.
Mundialmente, considerando-se todos os segmentos, podemos identificar quatro tipos de e-coat:
- E-coat anódico epóxi: apresenta moderada resistência à corrosão e baixa resistência à radiação ultravioleta. Empregado em implementos agrícolas, algumas peças automotivas e peças de fundição;
- E-coat anódico acrílico: utilizado como acabamento para aplicações de interiores. Oferece variações de cores e brilhos a baixo custo. Apresenta baixa resistência à corrosão e, por essa razão, o uso sobre ferro e aço depende de análise prévia de viabilidade. Empregado em mobiliário de escritório em metal (como estantes), difusores de ar e prateleiras;
- E-coat catódico epóxi: é referência em resistência à corrosão, muito superior quando comparado às outras famílias. O alto nível de resistência química também se destaca. É o produto de maior consumo no Brasil, respondendo quase que exclusivamente por toda a produção nacional. Normalmente do tipo epóxi-aromático, apresenta baixa resistência à radiação ultravioleta, demandando um acabamento protetivo para substratos sujeitos à radiação solar direta. Empregado por toda a indústria automotiva e de fornecedores de peças, além das indústrias geral e agrícola;
- E-coat catódico acrílico: da mesma forma que na versão anódica, apresenta variações de cores e brilhos, porém com maior resistência ao intemperismo natural e à corrosão. Empregado como acabamento em artigos de jardinagem, implementos agrícolas e rodas automotivas.
A química de formulação e eletrodeposição – Sistemas Catódicos
Deste ponto em diante, focaremos exclusivamente na eletrodeposição catódica de produtos à base de epóxi, dada sua importância no mercado brasileiro.
Um banho de e-coat é formado pela mistura de uma dispersão (emulsão de resina), de uma pasta pigmentada (normalmente cinza ou preta) e de água. A resina ou ligante (binder) é responsável pela criação de uma película protetiva capaz de manter o filme de tinta coeso, respondendo pelas principais características físico-químicas do filme, tais como resistência à corrosão ou ao intemperismo natural. A pasta pigmentada é composta por resinas, pigmentos e cargas, além de solventes, conferindo ao filme de tinta sua aparência, cor, poder de cobertura, brilho e parte de suas características reológicas. Dependendo de sua composição, também conferirá proteção anticorrosiva.
Além da dispersão de resina e da pasta, temos o terceiro componente do banho - a água deionizada - representando o meio líquido para a mistura e suspensão dos dois primeiros componentes. O sistema de eletrodeposição depende de água com um nível de qualidade que introduza a menor quantidade de íons possíveis ao banho. Garantir que elementos provenientes do pré-tratamento não sejam arrastados para o tanque de tinta (carry over) e assegurar água deionizada com um nível de íons abaixo de 20 ppm é uma condição crítica para assegurar uma operação estável do tanque de tinta. Finalmente, há um quarto grupo de componentes: os aditivos. Tratam-se de uma classe ampla, na qual cada material apresentará uma função específica, sendo sempre utilizados em pequenas quantidades. São exemplos: solventes orgânicos, para aumento de camada ou melhoria do aspecto do filme depositado; biocidas, para controle microbiológico e ácidos, para o controle de pH. Em linhas gerais, um banho poderia ser estratificado em água (80%); resina (15%); pigmentos e cargas (4%) e aditivos (1%).
A eletrodeposição de um revestimento orgânico sobre uma peça metálica é consequência de uma série de reações eletroquímicas. Três passos básicos são necessários para que a deposição ocorra: 1 - solubilização da resina em água; 2 - eletrólise da água; 3 - coagulação da resina.
As resinas catódicas para e-coat são insolúveis em água. Neutralizadas com um ácido carboxílico, ainda na fase produtiva, formam sais e se tornam solúveis em água:
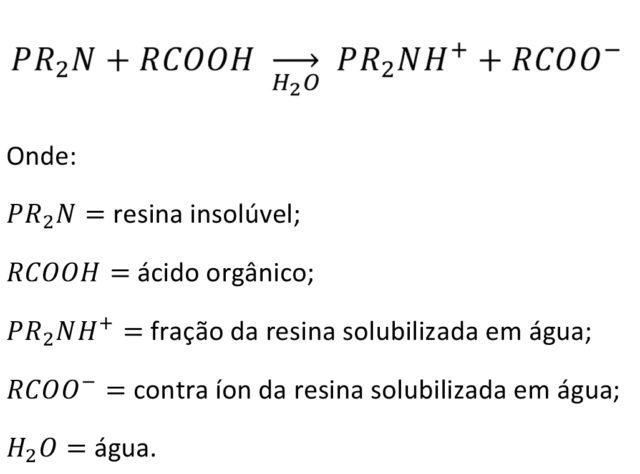
O sal da resina neutralizada (elemento central da emulsão de resina) atua como eletrólito no tanque de tinta, fornecendo a condutividade necessária para que a corrente migre através do meio aquoso.
A corrente elétrica inicia a decomposição da água no eletrodo (eletrólise), formando oxigênio (gás) e íons H+ no ânodo (ocorre a queda no pH ao redor do eletrodo), além de hidrogênio (gás) e íons OH- no cátodo (ocorre o aumento no pH ao redor da peça). As seguintes reações são estabelecidas:
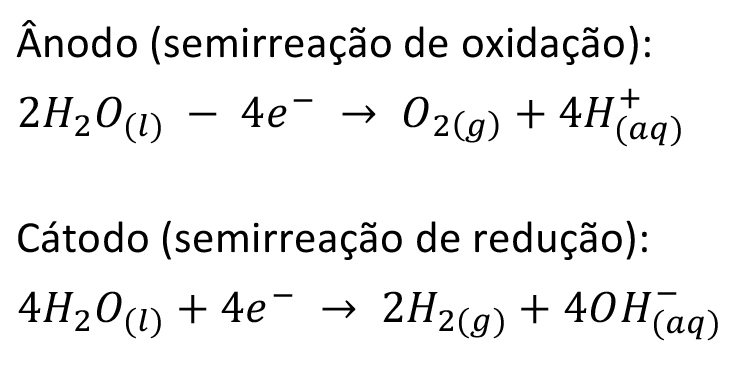
Uma vez gerada a diferença de potencial, a partícula de tinta inicia o processo de migração em direção ao objeto a ser pintado em um fenômeno denominado eletroforese.
Na última etapa do processo, os íons OH- gerados pela eletrólise no cátodo combinam com as partículas solúveis de resina, levando as partículas insolúveis que coagulam e recobrem uniformemente as superfícies em um processo denominado eletrocoagulação:

Lembre-se de que PR2N é a resina insolúvel que passa a constituir o filme eletrodepositado. A água intersticial e os eletrólitos são eliminados através de um fenômeno denominado eletro-osmose. O contra-íon da resina solubilizada migra para a célula anolítica (outro processo de eletroforese), combinando-se com o H+ gerado e mantendo a eletroneutralidade do sistema.
A diferença de potencial aplicada entre o ânodo (+) e o cátodo (-) é o parâmetro principal para o controle da espessura da película depositada sobre a superfície. O filme de tinta atua como um isolante elétrico; à medida que a espessura aumenta, também há o aumento da resistividade da superfície. Em um determinado instante, o processo de eletrodeposição cessa. Esta característica autolimitante da pintura é fundamental para assegurar a uniformidade do filme; além disso, à medida que regiões eletricamente ‘favorecidas’ (por exemplo, áreas externas da peça próximas ao eletrodo) tornam-se isoladas, outras regiões desfavorecidas assumem a continuidade do processo: é neste instante em que se inicia a pintura de regiões internas e cavidades. O grau em que uma tinta consegue penetrar e pintar áreas de difícil acesso recebe o nome de poder de penetração (throwpower).
Uma vez pintada, a peça é enxaguada para a remoção da tinta parcialmente coagulada (cream coat), a qual não adere efetivamente ao substrato, e depois segue para uma estufa, onde o filme passa por uma transformação química, tornando-se termofixo e atingindo todas as características de desempenho esperadas. Para tintas, essa transformação recebe o nome de cura.
Uma condição típica de cura é de 15 minutos a 175°C (temperatura-metal). Os detalhes e componentes de uma instalação para pintura de e-coat são tão ricos e interessantes que demandariam um artigo específico para abordagem e, por esse motivo, não aprofundaremos mais neste tema.
Os diferentes tipos de e-coat
Cada segmento produtivo apresenta uma série de requisitos que precisam ser integralmente atendidos. A evolução e a diversificação do e-coat epóxi catódico são consequências diretas dessas demandas. Podemos ressaltar três famílias principais conforme o setor aplicável:
A) E-coat convencional, para a indústria geral: Desenvolvido para englobar o maior número de processos produtivos possíveis, permite a obtenção de camadas relativamente altas (até 40 µm) e apresenta uma janela de cura bastante ampla para comportar as grandes variações observadas em campo. Uma janela é um gráfico que identifica em quais faixas de temperatura e tempo é possível curar uma determinada tinta e obter dela o melhor desempenho possível frente a determinada especificação de cliente. A Figura 1 exemplifica uma janela de cura típica. Qualquer ponto (dado por uma combinação de tempo e temperatura), situado dentro dos limites do polígono, representa uma condição aceitável para a cura do e-coat.
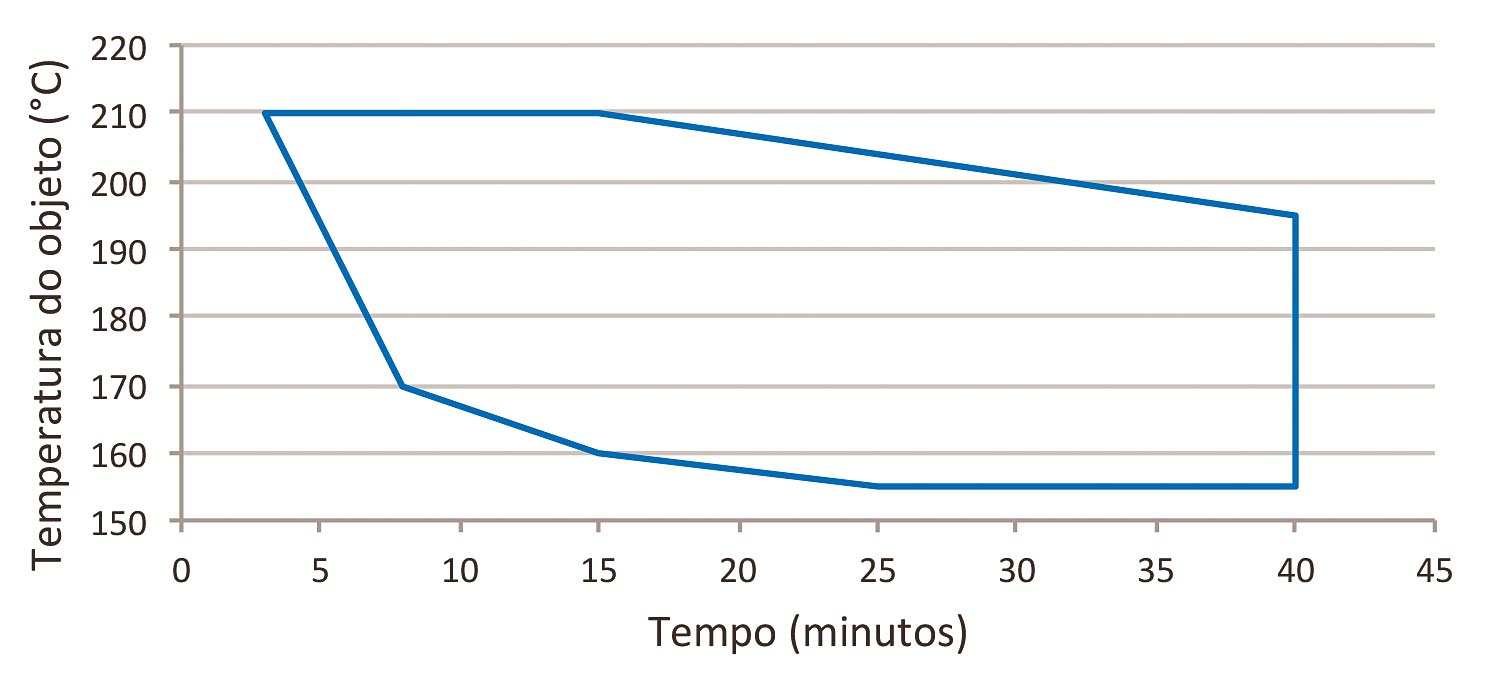
No segmento de indústria geral, a mesma tinta capaz de pintar peças para o segmento automotivo (rodas, trilhos de assentos, peças de reposição) é, em princípio, capaz de pintar esquadrias com a mesma qualidade e pouca variação em condições operacionais (como pH do banho, temperatura e condutividade). Ajustando-se o tempo e a tensão máxima de aplicação, é possível ajustar a espessura de camada desejada, normalmente acima de 18 µm.
Há também variações do sistema convencional para pintura a curas mais altas (normalmente por 20 minutos a 185 °C) sem comprometimento de características como flexibilidade ou dobramento do filme aplicado. Essas variantes encontram aplicação em implementos agrícolas pois indústrias que atuam nesse segmento normalmente pintam peças com alta variação de massa, onde uma unidade de poucos quilos é processada junto a outras pesando dezenas de vezes mais.
B) E-coat com alto poder de penetração, para montadoras: Diferentemente do e-coat para a indústria geral, a complexidade da peça a ser pintada (a carroceria) é significativamente superior. Fisicamente, o processo de eletrodeposição do e-coat é iniciado nas áreas externas da peça, onde há concentração de carga na superfície (Gaiola de Faraday). Enquanto essa região não se torna eletricamente resistiva, as áreas internas permanecerão sem pintura pois não desenvolverão carga apreciável. Se utilizássemos um produto com as mesmas características daquele dedicado à indústria geral, obteríamos uma camada externa muito alta em regiões externas da carroceria para atender às especificações de camada mínima para áreas internas ou de cavidade.
Pensando nesse cenário e visando assegurar a pintura de regiões de difícil acesso, tais como longarina e colunas, foi necessário o desenvolvimento de e-coats com alto poder de penetração. Isso é conseguido através de filmes que, uma vez depositados, isolam eletricamente a superfície a camadas relativamente mais baixas (boa capacidade autolimitante do sistema) quando comparados a sistemas convencionais, fazendo com que a diferença nas espessuras dos filmes nas áreas externa e interna seja minimizada. A vantagem? Redução significativa de consumo de tinta. Esses produtos são desenvolvidos, predominantemente, em banhos de cor cinza (ou, em poucos casos, preta), com grande penetração no mercado brasileiro e contando com homologações das maiores montadoras, tais como BW&P (modelos Mitsubishi), CAOA (Hyundai), Fiat, Ford, GM, Honda e VW.
C) E-coat com alta capacidade de proteção de bordas, para indústria de autopeças: Desenvolvido especificamente para conferir uma maior proteção de borda às peças pintadas. É normal observar que após o processo de cura as regiões de bordas apresentem menor espessura do filme. Quanto mais ‘afiadas’ forem essas bordas, menor será a camada na região. Uma série de fenômenos pode explicar essa diferença, mas normalmente diferenças de tensão superficial e contração do filme durante a reticulação são os mais comuns. É um diferencial para produtores de rodas e fornecedores de peças para montadoras de origem sul-coreana; nesses dois segmentos, camadas de bordas superiores representam proteção anticorrosiva adicional (proteção por barreira). A Figura 2 exemplifica o quanto isso pode impactar nos resultados de um teste de névoa salina, conforme ASTM B117 (240 horas). Há ainda o potencial de ganho em resistência à corrosão quando contemplamos superfícies com alta rugosidade, típicas de substratos à base de ferro fundido. Considerando o mesmo período e norma para exposição à névoa salina, a Figura 3 compara o produto desenvolvido para a proteção de bordas com um material comum disponível no mercado: nenhuma diferença é observada em uma superfície uniforme; ao contrário, a diferença de desempenho se faz notória nas regiões de alta rugosidade.
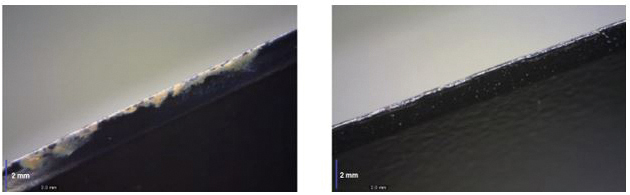
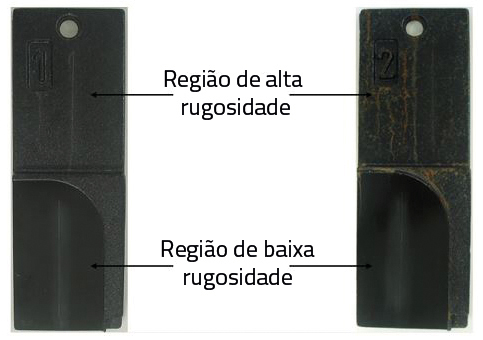
Conclusões
A pintura por eletrodeposição é um processo relativamente novo - considerando que o trabalho na década de 1960, sequer atingiu a marca de 60 anos. Com o avanço das legislações ambientais, o processo também se torna alternativa ecológica. Do ponto de vista de saúde e da segurança ocupacional, dada sua baixa toxicidade e não-inflamabilidade, também é uma alternativa a processos que ainda empreguem primers de imersão à base de solventes. Do ponto de vista econômico, graças ao seu alto grau de aproveitamento, é uma alternativa competitiva.
A indústria de tintas continua investindo em pesquisa e desenvolvimento de novas tecnologias capazes de oferecer maior rendimento e desempenho a preços competitivos, adequando-se e, quando possível, prevendo as principais demandas do mercado. O futuro continua promissor!
Referências
- Axalta Electrocoat Training Manual and Field Guide.
- Hans-Joachim Streitberger e Karl-Friedrich Dössel (editores); ‘Automotive Paints and Coatings’; 2ª edição (2008); WILEY-VCH Verlag GmbH & Co. KGaA, Weinheim; Capítulo 4.
- Cindy Oravitz (Diretor Executivo); ‘Electrocoating – A Guidebook for Finishers’; 1ª edição (2002); The Electrocoat Association, Cincinnati; Capítulo 2.
- Gary Orosz; ‘Basics of Electrocoating’ em ECOAT 2018; The Electrocoat Association (2018); Tampa; Boot Camp 101.
- Axalta, Boletim Técnico AquaEC 3000, revisão de 21/07/2016.
Acesse o conteúdo original publicado na revista Tratamento de Superfície, edição 217, página 30-35