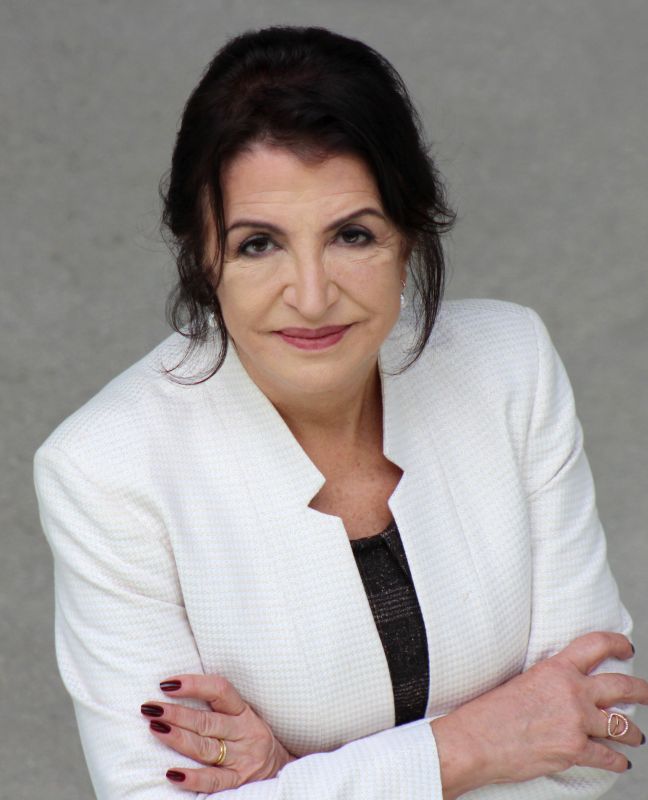
O presente trabalho é uma REPUBLICAÇÃO DA MATÉRIA TÉCNICA PUBLICADA NA REVISTA TRATAMENTO DE SUPERFÍCIE, EDIÇÃO 76, páginas 28 a 36, março/abril de 1996, realizada com o objetivo de abordar os vários aspectos envolvidos nos banhos de níquel tipo Watts. Ele está sendo publicado na forma de vários artigos cada qual tratando de um aspecto específico. Essa terceira parte tratará dos principais aditivos e influência das condições de operação.
1. PROPRIEDADES DOS BANHOS DE NÍQUEL
1.1 Eficiência de corrente catódica
A eficiência de corrente catódica dos banhos de níquel é relativamente alta (normalmente acima de 90 %). Praticamente em todos os tipos de banhos de níquel, a eficiência de corrente catódica é influenciada por outros parâmetros, a saber:
• temperatura: a eficiência de corrente catódica aumenta com o aumento da temperatura;
• densidade de corrente: a eficiência de corrente catódica aumenta com o aumento da densidade de corrente. A Figura 1 mostra a dependência entre estes dois parâmetros. Pode-se verificar que para baixos valores de densidade de corrente, pequenos aumentos da densidade de corrente determinam aumentos significantes da eficiência de corrente, porém para altos valores de densidade de corrente a interdependência entre estes dois parâmetros deixa de ser significativa;
• pH: a eficiência de corrente varia com o pH, atingindo os maiores valores na faixa de 3,5 a 4,5. A diminuição do pH, abaixo de 3,5 causa diminuição sensível da eficiência de corrente. O aumento do pH acima de 5 causa, também, diminuição da eficiência de corrente, porém pouco acentuado. Valores de pH acima de 5 não são usados, em geral, nos banhos níquel. Os banhos que contêm cloretos são menos sensíveis às variações de pH. Convém salientar que o pH é o parâmetro de maior importância para a eficiência de corrente;
• cloretos: a eficiência de corrente é maior nos banhos que contém apenas cloretos do que nos banhos do tipo Watts. Esta diferença é bastante significativa para baixos valores de densidade de corrente conforme ilustrado na Figura 2. Nos banhos de cloretos e sulfatos, um aumento da concentração de cloretos aumenta a eficiência de corrente. Deve-se ressaltar que a influência do cloreto não é muito significativa quando comparada à do pH e lembrar que os banhos que contêm cloretos, conforme já citado, são menos sensíveis às variações de pH;
• concentração de íons de níquel: a eficiência de corrente catódica aumenta com o aumento da concentração de íons de níquel no banho.
Figura 1 - Variação da eficiência de corrente com a densidade de corrente dos banhos de níquel. Nota-se que para densidades de corrente baixas a variação da eficiência de corrente A é muito maior do que a variação B observada para altas densidades de corrente.
Figura 2 - Comparação entre a eficiência de corrente catódica de banhos que contém só cloretos (?) e banhos tipo Watts (?), ambos com pH = 2.
1.2 Eficiência de corrente anódica
Nos processos de niquelação, há uma forte tendência de passivação dos anodos. No entanto, as condições de passivação são, na grande maioria dos casos, muito bem conhecidas de modo que na prática é raro deparar-se com problemas deste tipo. Caso ocorra a passivação, a eficiência anódica é praticamente nula, tendo-se uma condição em que os anodos de níquel se comportam como anodos inertes.
Na grande maioria dos processos de niquelação nos quais se utilizam condições compatíveis (tipo de anodo, tipo de banho e condições de operação), a eficiência de corrente anódica varia entre 97 % e 100 %. De uma maneira geral, a eficiência de corrente anódica aumenta com o aumento de temperatura e com aumento da densidade de corrente. No caso de anodos novos, eficiências menores podem ocorrer devido à presença de carepas na superfície deles.
Quanto à composição do banho, a maior influência é devida à presença de cloretos. No entanto, esta influência depende do tipo do anodo e do pH do banho.
No caso dos anodos que tendem a se passivar nos banhos de níquel, como é o caso dos anodos de níquel eletrolítico normal, a presença do íon cloreto torna-se imprescindível para se ter uma boa dissolução do anodo.
1.3 Poder de penetração
Os três principais fatores que afetam o poder de penetração dos banhos de eletrodeposição são: condutividade, polarização do catodo e dependência da eficiência de corrente com a densidade de corrente. Além desses fatores, o efeito de pontas é, também, muito importante. O poder de penetração dos banhos de níquel é muito mais baixo do que os banhos complexos (cianetados). As razões são:
• dependência da eficiência de corrente com a densidade de corrente: nos banhos de níquel, tem-se aumento da eficiência de corrente com o aumento da densidade de corrente, dependência esta inversa à dos banhos complexos. No caso do níquel, nas zonas de alta densidade de corrente praticamente toda a corrente é utilizada para depositar o níquel, enquanto nas zonas de baixa densidade de corrente, parte da corrente é utilizada na formação de gás hidrogênio;
• polarização catódica polarização catódica dos banhos de níquel é muito menor do que a dos banhos complexos.
Como consequência do baixo poder de penetração, mesmo em peças de geometria simples, têm-se grandes variações de espessura entre as zonas de alta densidade de corrente e as zonas de baixa densidade de corrente.
As condições de operação dos banhos de níquel têm pouca influência no seu poder de penetração, sendo o fator mais importante, conforme já citado anteriormente, a presença do íon cloreto. A adição de teores crescentes de cloreto melhora sensivelmente o poder de penetração, devido ao fato deste íon aumentar a condutividade dos banhos de níquel.
Uma melhora sensível na uniformidade da espessura, pode ser obtida utilizando-se técnicas como sombreamento, anodos conformados e ladrões.
2. PROPRIEDADES DOS ELETRODEPÓSITOS DE NÍQUEL
2.1 Aspereza
A causa da aspereza de camadas de níquel, obtidas a partir de banhos que operam com controle rigoroso do pH, é a presença, no banho, de partículas sólidas de dimensões relativamente grandes. Assim sendo, se cuidados forem tomados para evitar este tipo de contaminação, não se observará este tipo de problema.
2.2 Pites e poros
Pites são cavidades presentes na camada de níquel podendo ou não atingir o substrato. Em geral, são considerados pites aqueles visíveis a olho desarmado, porém, este conceito não é universal. Pites de dimensões microscópicas e que atingem o substrato são considerados poros.
Os pites e poros podem ter várias origens, a saber:
• formação de bolhas de gás hidrogênio;
• presença de óleos e/ou graxas na superfície do catodo devido a um pré-tratamento inadequado;
• presença de inclusões e/ou poros no substrato;
• incorporação de partículas sólidas pequenas o suficiente para não causar aspereza visível;
• adsorção temporária de partículas sólidas na superfície do catodo;
• formação de hidróxidos coloidais no filme catódico.
Nos processos modernos de níquel. não se têm pites devido à formação de bolhas de gás hidrogênio visto que, atualmente, têm-se disponíveis excelentes agentes tensoativos que eliminam por completo este problema.
Pites e poros devido a um pré-tratamento inadequado são facilmente evitáveis e controláveis, recomendando-se verificar continuamente a não ocorrência de quebra d’água na superfície do catodo antes de sua entrada no banho de deposição.
A formação de pites e poros devido a inclusões no substrato é contornada por meio de um controle de qualidade do próprio substrato.
Pites e poros devido à presença de partículas sólidas, introduzidas no banho por contaminação ou devido à formação de hidróxidos coloidais também podem ser controlados. O primeiro deve ser evitado investigando-se a fonte de contaminação. O segundo deve ser evitado por meio da manutenção rigorosa do pH dentro da faixa especificada, de preferência igual ou pouco inferior a 4, e o controle rigoroso de impurezas, principalmente de íons de metal alcalino como sódio ou potássio, que agravam a tendência de aumento de pH na interface catodo/banho.
2.3 Fissuras
As fissuras nas camadas de níquel são formadas nos casos em que se têm, concomitantemente, as seguintes condições:
• perfeita aderência na interface substrato/revestimento;
• alto nível de tensões de tração internas;
• camadas de níquel frágeis.
Nessas condições, para aliviar as tensões de tração, a camada de níquel frágil sofre trincamento, o que determina o aparecimento das fissuras.
Se a aderência fosse precária, o alívio das tensões ocorreria por destacamento da camada de níquel. Se o níquel fosse dútil, o alívio de tensões ocorreria ou por deformação da camada ou através de aparecimento de falhas no substrato.
2.4 Porosidade
Define-se como porosidade toda descontinuidade capaz de expor o substrato.
Deve-se considerar as duas formas de porosidade: a intrínseca e aquela devida às condições operacionais e o grau de pureza dos banhos. Nessa última categoria, pertencem as já discutidas como poros, pites e fissuras. Portanto um controle rigoroso do processo poderá minimizá-la, ou mesmo eliminá-la completamente.
Já a porosidade intrínseca, manifestada, em geral, na forma de pequenos poros, estará sempre presente sendo altamente dependente da espessura do revestimento e da natureza e do tipo de acabamento de superfície do substrato. Camadas finas, invariavelmente, apresentam poros. aumentando-se a espessura da camada, a porosidade vai diminuindo. A intensidade desta diminuição depende do acabamento superficial do substrato. Experiências mostram que 5 ?m de níquel depositado sobre cobre polido, em condições controladas, não apresentam poros. Já camadas depositadas nas mesmas condições sobre aço não polido, mas lixado com lixa de grana 240, deixam de apresentar poros somente após 25 ?m a 30 ?m de espessura.
2.5 Aderência
Na realidade, a aderência não é uma propriedade intrínseca do eletrodepósito, mas está relacionada com a “força de ligação” do eletrodepósito com o substrato.
As causas de falta de aderência dos eletrodepósitos de níquel são muitas, sendo as mais relevantes apresentadas a seguir:
• pré-tratamento inadequado: esta é a causa mais comum nos processos de niquelação. Qualquer sujidade presente na superfície do catodo poderá determinar falta de aderência. Resíduos de óleos ou graxas, óxidos ou quaisquer tipos de produtos de corrosão, resíduos de desengraxantes ou de outras soluções utilizadas no ciclo de pré-tratamento são capazes de causar a má aderência dos depósitos de níquel. O teste de “quebra d’água” é muito útil para verificar a limpeza da superfície do catodo, principalmente no que se refere à presença de óleos ou graxas ou produtos de corrosão. No entanto, esse teste não é capaz de detectar a presença de contaminações com os produtos utilizados no pré-tratamento, como desengraxantes;
• porosidade e defeitos superficiais do substrato: poros ou defeitos superficiais presentes no substrato podem reter os produtos utilizados no ciclo de pré-tratamento (como desengraxantes e decapantes). Tais produtos podem exsudar após a deposição do níquel, causar a corrosão do substrato na interface substrato/níquel e determinar o destacamento da camada de níquel. Esse tipo de problema, normalmente, é detectado após decorrido um certo tempo;
• aços com alto teor de carbono ou ferro fundido: quando o teor de carbono do substrato é muito elevado, durante a decapagem, forma-se sobre a superfície do substrato um filme de cementita ou de grafita, devido ao ataque preferencial da ferrita. Esse filme não é removido durante a operação de lavagem subsequente, de modo que o substrato atinge o tanque de deposição com um filme superficial. O níquel depositado sobre esse filme não é aderente. Para se evitar ou minimizar esse tipo de problema, deve-se evitar decapar substratos com alto teor de carbono com ácidos concentrados. Deve-se utilizar ácidos diluídos contendo inibidores de corrosão ou utilizar ácido fosfórico;
• excesso de abrilhantador secundário: a literatura cita que um excesso de abrilhantador secundário causa falta de aderência das camadas de níquel. Nenhuma explicação foi encontrada para esse fato;
• deposição por deslocamento galvânico: quando uma peça de aço é mergulhada num banho de níquel, mesmo sem a aplicação de corrente externa, ocorre a deposição de níquel devido à corrosão do aço. Esse fato é denominado DEPOSIÇÃO POR DESLOCAMENTO GALVÂNICO. As reações responsáveis por essa deposição e o provável valor de seus respectivos potenciais de equilíbrio são:
Os elétrons necessários para a reação de deposição de níquel são fornecidos pela reação de corrosão do ferro. Isso ocorre, devido ao fato do níquel, num banho de níquel tipo Watts, ter um potencial de equilíbrio muito maior do que o do ferro. As camadas de níquel obtidas por deslocamento galvânico, em condições de grandes diferenças de nobreza, são pouco aderentes. À medida que se diminui a diferença de nobreza (diferença entre os potenciais de equilíbrio) melhora a aderência do depósito de níquel. Convém lembrar que, uma vez obtido um depósito não aderente, camadas eletrodepositadas, obtidas após a aplicação de correntes externas, não serão aderentes. A situação ideal é abaixar o potencial de equilíbrio do níquel para um valor inferior ao do ferro. Nessas condições, cessa por completo a deposição por deslocamento galvânico, passando-se para uma condição apenas de eletrodeposição, ou seja, o níquel só deposita com passagem de corrente externa. Uma outra maneira de minimizar a deposição por deslocamento galvânico é a “entrada viva”, ou seja, a introdução do catodo no banho já conectado à fonte de corrente. Com isso, a peça já entra no banho com potencial de sua interface abaixo do potencial de equilíbrio do ferro, evitando assim a sua corrosão. No caso específico do níquel a deposição por deslocamento galvânico não é muito pronunciada de modo que a “entrada viva” normalmente elimina por completo esse tipo de problema;
• interrupção da deposição: durante a eletrodeposição, se por algum motivo (interrupção de corrente ou parada de produção) ocorrer interrupção prolongada de deposição de níquel, a camada já depositado poderá passivar-se. Se, em seguida, tentar-se continuar a deposição haverá falta de aderência. Note que essa falta de aderência não ocorre na interface substrato/depósito, mas entre as camadas de níquel. É conveniente ressaltar que a velocidade de passivação do níquel é lenta, de modo que paradas rápidas não representam problema.
A falta de aderência pode ser detectada submetendo-se os produtos niquelados aos testes de aderência. No entanto, essa falta de aderência pode, em casos extremos, manifestar-se na forma de empolamento ou destacamento, visíveis a olho desarmado. O empolamento aparece em camadas muito dúteis e o destacamento em camadas frágeis. Ambos os defeitos podem aparecer tanto devido à formação de bolhas de gás hidrogênio na interface substrato/revestimento não aderente como devido à presença de alto nível de tensões na camada de níquel. Deve-se lembrar o fato já mencionado de que, nos casos em que se tem depósitos aderentes, o alto nível de tensões na camada de níquel causa fissuramento e não destacamento.
Convém discutir o fato de que, na prática, muitas vezes é verificado desplacamento de camadas de níquel nas zonas de alta densidade de corrente, principalmente nos processos brilhantes. Razões para a ocorrência deste fato não foram encontradas na literatura, a despeito de intensas consultas. Baseado nos conhecimentos teóricos sobre os mecanismos de ligação revestimento/substrato e sobre o fato das zonas de alta densidade de corrente apresentarem maiores tensões internas, levantaram-se algumas hipóteses que pudessem explicar a ocorrência do fato em questão.
No início de qualquer processo de eletrodeposição, os átomos do metal que estão sendo depositados tendem a se arranjar da mesma maneira que os átomos do substrato, ou seja, há uma tendência dos cristais dos eletrodepósitos continuarem a estrutura cristalina do substrato. Esse tipo de crescimento é denominado de crescimento epitaxial. A tendência do crescimento epitaxial diminui com o aumento da espessura da camada. A intensidade com que esse fenômeno ocorre depende de muitos fatores, podendo-se citar:
• natureza do substrato: a tendência do crescimento epitaxial aumenta nos casos em que o substrato e o revestimento possuem estruturas cristalográficas similares;
• densidade de corrente: quanto menor for a densidade de corrente de deposição, maior é a tendência do crescimento epitaxial;
• temperatura: quanto maior a temperatura, maior é a tendência do crescimento epitaxial;
• presença de impurezas e/ou de aditivos: quanto maior a pureza do banho (menor concentração de impurezas e de aditivos), maior a tendência do crescimento epitaxial.
Nos casos em que ocorre crescimento epitaxial, a ligação entre os átomos do substrato e do revestimento é muito forte, sendo excelente a aderência. Quando o crescimento epitaxial não ocorre, a aderência é devida às forças do tipo Van der Walls, forças iônicas e forças polares, que apesar de garantirem aderência satisfatória, são mais fracas.
Como o aumento da densidade de corrente de deposição e o aumento da concentração de aditivos diminuem a tendência do crescimento epitaxial, é possível que as forças de ligação na interface substrato/revestimento sejam menores nas zonas de alta densidades de corrente dos depósitos obtidos a partir de banhos brilhantes. Além disso, nas zonas de alta densidade de corrente, pode haver uma situação em que a corrente aplicada ultrapasse a densidade de corrente limite, o que causa a formação de depósitos queimados. Um outro fator de extrema importância que ocorre nas zonas de alta densidade de corrente é o aumento do nível de tensões de tração internas, principalmente na presença de altos teores de abrilhantador secundário.
Face ao exposto, pode-se supor que o destacamento nas zonas de alta densidade de corrente ocorra devido ao fato da ligação entre o substrato e o revestimento ser suficientemente fraca nestas regiões, a ponto de as tensões internas serem capazes de vencê-la e determinar a separação entre o substrato e o revestimento.
2.6 Queima de depósitos
É muito comum, nos processos de eletrodeposição, a obtenção de depósitos pulverulentos e escuros nas zonas de alta densidade de corrente. Esse tipo de depósito é conhecido como depósito queimado e ocorre quando as densidades de corrente ultrapassam o valor da densidade de corrente limite, o que determina uma diminuição substancial da eficiência de corrente devido ao aumento da ocorrência de outras reações de redução do catodo, principalmente da reação de redução de hidrogênio.
A formação de depósitos queimados, nessas condições, é devida a uma ou mais dos seguintes fatores:
• aumento da velocidade de nucleação o que, por si só, favorece a formação de depósitos pulverulentos;
• aumento considerável da quantidade de cátion hidrogênio reduzido no catodo, o que ocasiona rápido aumento do pH na interface catodo/banho. Como consequência tem-se excessiva formação e incorporação de hidróxidos metálicos no depósito. Tais depósitos terão alto nível de tensões internas. Além disso, a tendência de formação de depósitos de granulação muito fina aumentará, tornando-se pulverulentos;
• incorporação no depósito de moléculas de água devido ao fato de se ter uma situação em que a velocidade de perda das moléculas de água de solvatação tornar-se mais lenta do que a velocidade de incorporação dos ad-íons no depósito.
2.7 Composição do eletrodepósito
Eletrodepósitos obtidos a partir de banhos devidamente purificados, praticamente não contêm impurezas metálicas, exceção feita ao cobalto. No entanto, se o banho não for controlado adequadamente, as impurezas metálicas codepositar-se-ão, sendo a porcentagem relativa das impurezas maior nas zonas de baixas densidades de corrente.
Além de íons metálicos, as camadas de níquel contêm hidrogênio, oxigênio, carbono e enxofre em concentrações que variam em função das condições de operação e da natureza dos aditivos utilizados, conforme discutidos a seguir.
2.7.1 Presença de cobalto no eletrodepósito
Todos os eletrodepósitos de níquel obtidos a partir de banhos preparados com sais de pureza comercial e anodos de níquel eletrolíticos conterão cobalto. Isto porque os minérios de níquel contêm cobalto. Como esses dois elementos estão localizados muito próximos na Tabela Periódica e, portanto, possuem propriedades físico-químicas semelhantes, a separação do cobalto é muito difícil. Assim sendo, os sais e anodos de níquel contêm cobalto como impureza e este íon metálico não pode ser eliminado do banho pelos processos normais de purificação (carvão ativo e deposição seletiva). Não se pode afirmar qual a quantidade exata de cobalto presente no eletrodepósito de níquel, pois isto dependerá da qualidade dos sais e anodos utilizados, no entanto, pode-se dizer que é da ordem de 0,5 % a 2 %.
O teor de cobalto no depósito será tanto maior, quanto maior for o nível de contaminação das matérias primas. Variações de temperatura, pH e composição não afetam muito o teor de cobalto do depósito, no entanto, a densidade de corrente tem influência sensível. O teor de cobalto é bastante elevado nas zonas de baixa densidade de corrente diminuindo drasticamente com o aumento da densidade de corrente.
As propriedades mecânicas são pouco influenciadas devido à presença de cobalto, nos teores presentes como impurezas. No entanto, a resistividade elétrica dos depósitos sem cobalto é significativamente menor do que a resistividade de depósitos com cobalto. Deve-se lembrar que a medida da resistividade é uma das maneira de controlar a pureza dos eletrodepósitos. A Figura 3 ilustra a influência do teor de cobalto na resistividade.
FIGURA 3 - Aumento da resistividade dos depósitos de níquel com o aumento do teor de cobalto
2.7.2 Presença de hidrogênio e oxigênio no eletrodepósito
Camadas de níquel eletrodepositadas contêm uma pequena quantidade de hidrogênio e oxigênio (da ordem de 0,001 % a 0,01 % de hidrogênio e 0,003 % a 0,046 % de oxigênio).
O hidrogênio pode penetrar na camada tanto como hidrogênio atômico como na forma de hidróxido coloidal. Acredita-se que esta segunda forma seja mais provável. Já para o caso do oxigênio, acredita-se que sua presença é devida quase que exclusivamente à presença de hidróxidos coloidais.
Os teores de oxigênio e hidrogênio variam com as condições de operação. Os fatores mais significativos são:
• temperatura: ocorre uma diminuição dos teores de hidrogênio e oxigênio com o aumento da temperatura;
• densidade de corrente: o teor de oxigênio e hidrogênio é bastante elevado para densidade de correntes muito baixas (abaixo da faixa operacional). Com o aumento da densidade de corrente (até aproximadamente 2 A/dm2) ocorre uma queda brusca. A partir deste valor, incluindo a faixa operacional, verifica-se um aumento do teor de hidrogênio e oxigênio com o aumento da densidade de corrente (ver Figura 4);
• pH: é o fator mais significativo. O teor de hidrogênio e oxigênio aumenta continuamente com o aumento do pH, no entanto, a partir do pH 5, o aumento torna-se muito mais acentuado, devido ao favorecimento da precipitação dos hidróxidos coloidais (ver Figura 5).
FIGURA 4 - Efeito da densidade de corrente sobre os teores de hidrogênio e de oxigênio nos eletrodepósitos de níquel.
FIGURA 5 - Efeito do pH sobre os teores de hidrogênio e de oxigênio nos eletrodepósitos de níquel (média de 26 depósitos obtidos a partir de diferentes banhos, diferentes temperaturas e densidades de corrente),
2.7.3 Presença de cloreto no eletrodepósito
Os depósitos de níquel contêm cloretos em teores que variam de 0,005 % a 0,025 %. Acredita-se que o cloreto é incorporado como sal básico. A presença de um ânion no depósito pode parecer estranho, uma vez que o cloreto sendo um ânion (portanto possui carga negativa) não deveria ser adsorvido sobre o eletrodo negativo. No entanto, o cloreto é um íon que apresenta grande capacidade de adsorção específica, o que explica este fato.
2.7.4 Presença de enxofre no eletrodepósito
Depósitos de níquel contêm teores variados de enxofre. Acredita-se que esse enxofre é proveniente, principalmente, dos aditivos, que contêm este elemento na sua composição, e não do íons sulfato. Em geral, o enxofre está presente no eletrodepósito na forma de sulfeto de níquel.
Os abrilhantadores primários são as principais fontes de enxofre, mais do que os secundários. Os agentes tensoativos também são considerados fontes de enxofre.
Os depósitos de níquel fosco obtidos a partir de banhos tipo Watts não aditivados (a menos de agentes tensoativos) contêm teores de enxofre inferiores a 0,005 % e os depósitos de níquel semibrilhantes obtidos a partir de banhos com aditivos isentos de enxofre (a menos dos agentes tensoativos) contêm teores de enxofre inferiores a 0,01 %.
Depósitos de níquel brilhante são quase sempre obtidos a partir de banhos com aditivos que contêm enxofre (abrilhantadores primários e alguns tipos de abrilhantadores secundários). Por essa razão, esses contêm teores de enxofre mais elevados variando de 0,03 % a 0,08 %. No entanto, valores maiores podem ser encontrados, tendo sido já citado na literatura teores de até 6 %.
O teor de enxofre nos depósitos depende principalmente do tipo e da concentração do aditivo. No entanto, as condições de operação, também, exercem certa influência sendo a densidade de corrente o fator mais significativo. O teor de enxofre decresce como o aumento da densidade de corrente.
A presença de teores elevados de enxofre torna o depósito mais frágil. Acredita-se que essa fragilidade é devida à formação, em contorno de grão, de sulfetos de níquel. A literatura cita, ainda, que depósitos de níquel brilhante (com teores elevados de enxofre) submetidos a tratamentos térmicos tornam-se mais frágeis. Além disso, como o ponto de fusão desses sulfetos é baixo (~ 630 ?C), verifica-se a perda de resistência mecânica desses revestimentos em altas temperaturas.
2.7.5 Presença de carbono no eletrodepósito
Depósitos de níquel obtidos a partir de banhos que contêm aditivos orgânicos contêm carbono. Na ausência de aditivos, não se verifica a presença deste elemento.
O teor de carbono varia principalmente com o tipo de aditivo, oscilando, em geral, entre 0,02 % a 0,1 %.
Dentre as condições de operação, a densidade de corrente exerce a maior influência. De maneira semelhante ao enxofre, o teor de carbono diminui com o aumento da densidade de corrente.
BIBLIOGRAFIA CONSULTADA
BRUGGER, R. Nickel plating. 1.ed. Teddington : Robert Draper, 1970. 363p.
DENNIS, J. K.; FUGGLE, J. J. The effect of metallic contamination on electrodeposited nickel: part 2 - appearance and surface topography. Transactions of the institue of metal finishing, v.48, 1970. p.75-82
DENNIS, J. K.; SUCH, T. E. Nickel and chromium plating. 1.ed. London : Newnes-Butterworths, 1972. 324p.
KUSHNER, J. B. Electroplating know how II: lesson 8. 1972 47p.
LOWENHEIM, F. A. Modern electroplating. 3ed. New York : John Wiley, 1974. 801p.
METAL FINISHING. New Jersey : Metals and Plastics Publications, v.8, n.12, dec. 1989. 76p.
METALS handbook. 9ed. Metals Park : ASM, 1987. 17v. v.5 : surface cleaning, finishing and coating. 715p.
OGBURN, F.; ERNST, D. W.; ROBERTS, W. H. The nature, cause and effect of porosity in electrodeposits. AES research project, n.13, Washington : AES
PANOSSIAN, Z. Corrosão e proteção contra corrosão em equipamentos e estruturas metálicas. 1.ed. São Paulo : Instituto de Pesquisas Tecnológicas, 1993. 2v. 636p. (Publicação IPT 2032)
PANOSSIAN, Z. Mecanismos de eletrodeposição de metais. (não publicado)
PRATICAL Nickel plating. New York : INC. 56 p.
SAFRANEK, W. H. Properties of electodeposited metals and alloys : a handbook. New York : American Elsevier, 1974. P.219-288
WATSON, S. A. Nickel electroplating solutions. England : NiDi, 1989. (NiDi technical series n. 10047)
WESLEY, W. A.; PRINE, W. H. Pratical nickel plating. New York : INC. 44p.
ZAMIN, M.; IVES, M. B. Effect of chloride concentration on the anodic dissolution behaviour of nickel. Corrosion, NACE, v.29, n.8, Aug., 1973. p.319-324
ZENTNER, V.; BRENNER, A.; JENNING, C. W. Physical properties of electrodeposited metals : I. nickel. Washington : AES, 1952. (Serial n.20)