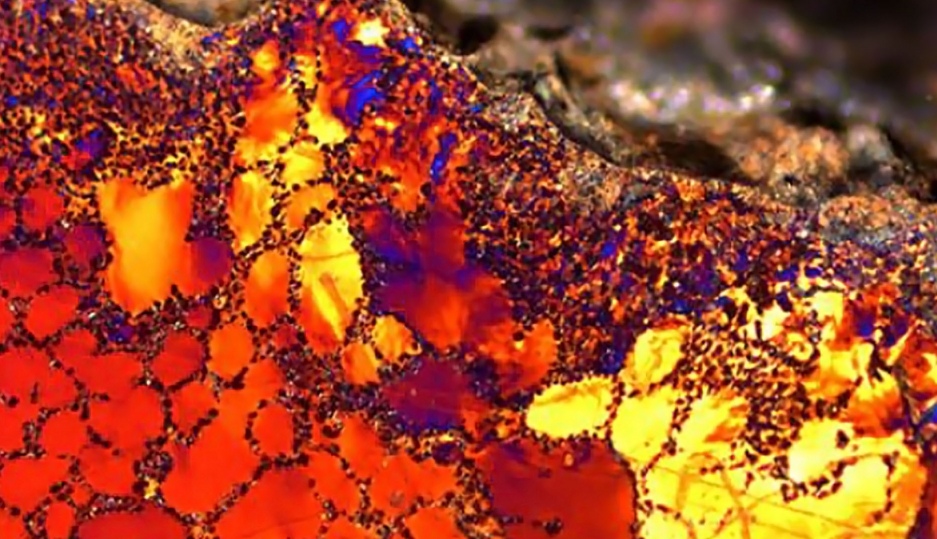
Pesquisa de novo processo consegue mostrar como criar condições ideais para anodizar peças de alumínio fundido com alto teor de silício
Diretor Técnico da Coventya Politeknik
Tuzla Kimya Sanayicileri Organize San. Bolgesi
Kristal Cad. No : 2 Tuzla/Istambul - TURQUIA
c.akyl@coventya.com
ABSTRACT
For the success of the electric cars, the weight reduction is the key, which makes especially cast aluminum parts become more important due to their excellent weight to strength ratio. However, the amphoteric character of aluminum, without some treatment makes its use not practical in many industries including automotive applications. The anodizing process is a common treatment for providing many important properties to aluminum substrates. Per nature, anodizing quality is strongly affected by the factors governing the dissolution of aluminum such as alloying elements like silicon. These elements are needed to enhance the physical properties like castability; at the same time causing the discontinuity of the anodic oxide film, inhomogeneous thickness distribution, low hardness and decreased seal quality.
This study aims to create optimum conditions to anodize cast aluminum parts with high silicon content by revealing the relation between the morphology/distribution of the intermetallics and anodic oxide film attributes with optical microscopy, SEM and EDS mapping. The quality of the anodized layers will be quantified by using potentiostatic methods, salt spray tests, acidic dissolution tests and SEM analyses.
RESUMO
Para o sucesso dos carros elétricos, a redução de peso é a chave, fazendo com que especialmente as peças de alumínio fundido se tornem mais importantes devido à sua excelente relação peso/força. No entanto, o caráter anfótero do alumínio, sem algum tratamento, torna seu uso pouco praticável em muitos setores, incluindo aplicações automotivas. O processo de anodização é um tratamento comum para fornecer muitas propriedades importantes aos substratos de alumínio. Por natureza, a qualidade da anodização é fortemente afetada pelos fatores que governam a dissolução do alumínio e dos elementos de liga, como o silício. Esses elementos são necessários para aprimorar as propriedades físicas, como a fusibilidade; causando ao mesmo tempo a descontinuidade do filme de óxido anódico, distribuição não homogênea da espessura, baixa dureza e diminuição da qualidade da selagem. Este estudo tem como objetivo criar condições ideais para anodizar peças de alumínio fundido com alto teor de silício, revelando a relação entre a morfologia/distribuição dos elementos intermetálicos e do filme de óxido anódico, através de microscopia óptica, mapeamento MEV (microscópico eletrônico de varredura) e EDS (espectro de energia dispersiva). A qualidade das camadas anodizadas será quantificada utilizando métodos potenciostáticos, testes de névoa salina, testes de dissolução ácida e análises MEV.
Existe, hoje, uma ênfase em muitas plataformas industriais, especialmente na indústria automotiva, na utilização de materiais de menor peso. As ligas de alumínio são a escolha ideal para substituir componentes pesados, incluindo aqueles tradicionalmente fabricados por processos de fundição de aço.
As ligas de alumínio fundido, devido à sua excelente razão peso/resistência, estão encontrando novas aplicações em muitas áreas, produzindo menores emissões de gases de efeito estufa e ajudando a atender aos requisitos das normas de eficiência energética. Essas ligas, ricas em espécies intermetálicas, são uma das alternativas utilizadas em aplicações automotivas para a substituição de peças e componentes de aço.
Além disso, a redução de peso também é um dos objetivos principais para as plataformas de mobilidade elétrica. Os desafios atuais incluem limitações pela capacidade da tecnologia de baterias existente – porque esses sistemas respondem por grande parte do peso dos veículos elétricos. É importante que a identificação de outras áreas de redução de peso seja considerada pelos fabricantes de automóveis a fim de maximizar a duração da viagem para essas plataformas competirem com a tecnologia de motores a gasolina. No entanto, o alumínio como todos os outros metais, torna-se suscetível à corrosão (principalmente corrosão por pitting) na presença de íons agressivos ou sob condições ambientais específicas.
Calor, frio e umidade fornecem condições para potencial corrosão acelerada. Outros exemplos incluem detergentes em sistemas automáticos de lavagem de carros ou quando aditivos são utilizados para derreter neve e gelo em estradas e rodovias durante os meses de inverno (em países com essa realidade). Para substituir os sistemas atuais dos revestimentos nos componentes em aço, esses componentes automotivos fabricados em alumínio e suas ligas têm a necessidade de fornecer alto desempenho contra a corrosão. O processo de anodização, ou ‘oxidação anódica’ do alumínio, é um dos meios mais eficientes e eficazes para fornecer boa proteção contra corrosão e alto desempenho para essa gama de ligas.
Com o objetivo de melhorar essa performance, foi desenvolvido um processo para otimizar as condições de anodização de peças de alumínio fundido com altas concentrações de silício. Levando em conta a morfologia/distribuição das espécies intermetálicas e sua interferência sobre a qualidade do filme de óxido anódico, os resultados demonstram aperfeiçoamento do processo de anodização, minimizando essa interferência e, ao mesmo tempo, melhorando a qualidade da camada de Óxido de Alumínio Anódico (AAO).
Novo processo para estudo
As avaliações metalúrgicas das superfícies anodizadas, e da liga anodizada A356, foram feitas com os métodos de Microscopia Óptica (OM), Microscopia Eletrônica de Varredura (MEV) e Teste de Névoa Salina Neutra (NSS), de acordo com a norma ASTM B - 117/ISO 9227. Esses métodos permitem a verificação dos resultados comparados com os do processo otimizado.
A liga de alumínio fundido frequentemente utilizada para substituir componentes em aço para aplicações externas é a ISO AlSi7Mg, comumente conhecida como ASTM A356. Isso é equivalente ao SAE 323, ou EN AL 42100, que representa uma liga de alta resistência para uso geral e exibe boas propriedades para fundição – particularmente utilizada na fabricação de peças sujeitas a cargas cíclicas ou vibratórias. Essa liga é reconhecidamente ideal para a fabricação de peças de design complexo, incluíndo componentes de paredes finas usadas em diversos setores como: ferroviário, aeronáutico, mecânico e automobilístico (sistemas de bombeamento e sistemas de motores de combustão são alguns exemplos).
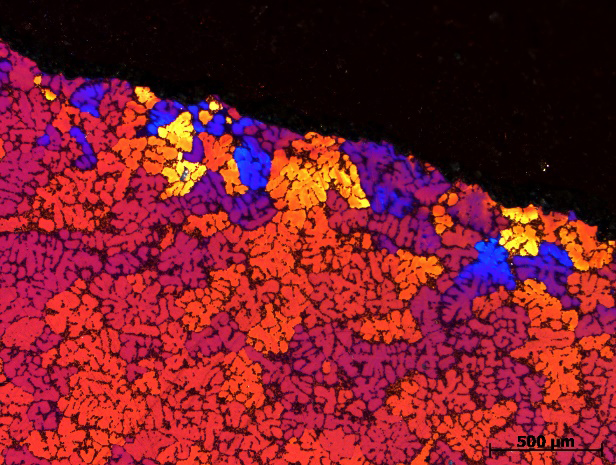
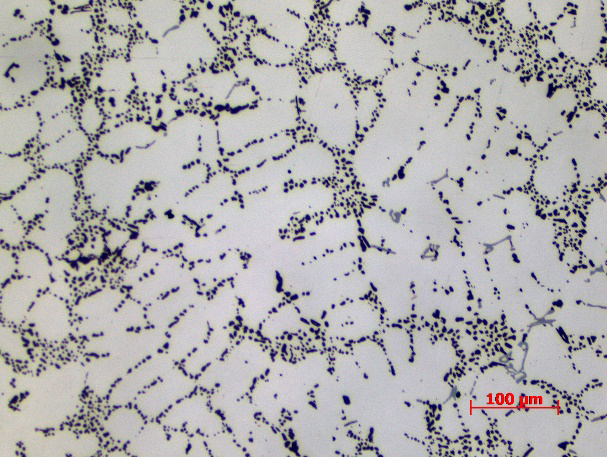
Figura 1: Estudo do corte transversal das amostras de liga AlSi7Mg (A356).
Conforme mostrado na imagem polarizada (Figura 1a), com ampliação de 50X, devido ao processo de fundição e à taxa de resfriamento mais rápida nas paredes do molde de fundição sob pressão, os grãos são menores do que os mais próximos do centro da amostra. Já a Figura 1b) demonstra a distribuição das fases secundárias nas amostras, com ampliação de 100X, com a forma e distribuição típicas dos moldes de fusão hipoeutéticos permanentes.
O silício, uma importante espécie intermetálica, é propositalmente introduzido no interior da liga do alumínio para melhorar o processo de fundição sob pressão. Isso favorece o trabalho de formas e geometrias complexas de peças a serem fabricadas. No entanto, a presença de altas concentrações e gradientes de silício em toda a liga de alumínio, denominadas de ‘rios de silício’ – mostrados na fotomicrografia 1a) – pode criar problemas no processo de anodização e no desempenho da resistência à corrosão pós-anodização. Ligas com maiores concentrações de silício podem inibir o crescimento de filmes de óxido anódico em condições galvanostáticas e potenciostáticas.
Para estudar e melhor mostrar o efeito do resfriamento na morfologia da superfície e no crescimento de óxidos, um avançado método é usado: as amostras são primeiramente cortadas em ângulo de 15 graus, e preparadas para micrografia óptica, de modo que a parte superior das imagens esteja realmente entre a interface da camada de óxido e o substrato metálico.
A Figura 2 representa uma microscopia polarizada com ampliação de 200X de uma liga A356 anodizada, processada a 15ºC por 20 minutos em um eletrólito contendo 5% de ácido oxálico e 17% de ácido sulfúrico (eletrólito GSX). Os pequenos cristais densos, no topo da fotomicrografia, representam a camada anodizada. O alumínio e as espécies intermetálicas, incluindo o silício, são representados na seção transversal pelos grãos maiores na imagem. Pode-se verificar que as zonas concentradas intermetálicas de silício, que podem ser vistas a olho nu, impedem a formação uniforme da camada de óxido de anodização.

Além disso, essas áreas de maiores concentrações de silício causam menor dureza do óxido e afetam negativamente a qualidade/eficiência da selagem pós-anodização. Essas são considerações importantes para o desempenho geral da corrosão da camada AAO. Sob o filme de óxido anodizado formado, o silício também atua como par galvânico de modo a iniciar o fenômeno de pitting ou causar outros tipos de falhas de corrosão localizada, o que é prejudicial ao uso do alumínio para muitas das aplicações externas.
Otimizando o ciclo de processo de anodização
Levando em conta todas essas considerações, foi desenvolvido um trabalho para otimizar o ciclo do processo de anodização de peças fundidas de alumínio que demonstrou grande sucesso no desempenho e na qualidade.
Para validar esses resultados, e demonstrar a melhoria do processo desenvolvido, foram utilizadas técnicas de microscopia óptica e SEM/EDS. Para complementar os ensaios, também foram feitos testes de Névoa Salina Neutra, Salt-Spray (NSS). Para essas avaliações, as amostras foram anodizadas diretamente em um eletrólito à base de ácido sulfúrico (170 g/L), a 15º C, com diferentes aditivos orgânicos projetados para limitar o efeito inibidor do silício – que faz com que a camada anodizada seja descontínua. Após anodizadas, as amostras de liga A356 foram coloridas com um pigmento orgânico preto a 65º C por 15 minutos. Posteriormente, foram seladas a frio em solução à base de fluoreto de níquel; pH a 5,9; 33º C, por 15 minutos, seguidas por imersão em água quente a 65º C. A TABELA 1 fornece uma visão detalhada do ciclo operacional utilizado.
TABELA 1: Sequência do processo para as amostras A, B, C e D (incluindo amostras com uso de pigmentos para os testes de NSS)
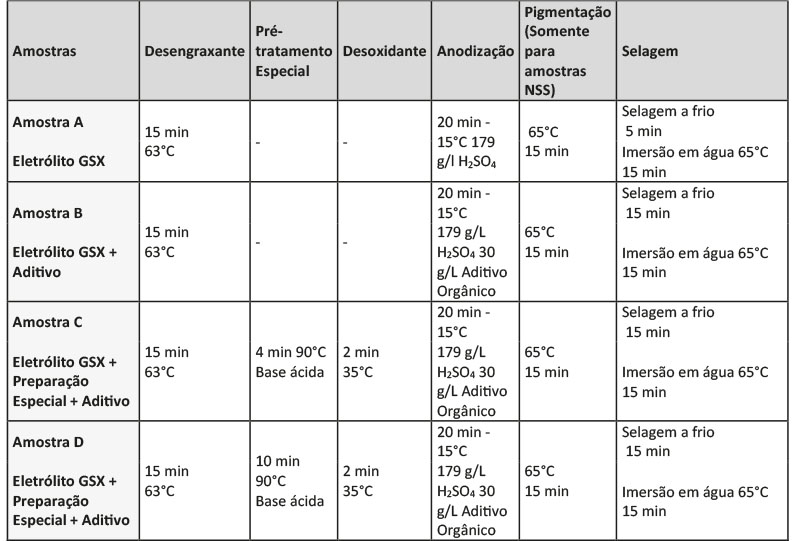
Para superar os problemas causados por concentrações muito altas de silício na liga de fundição e obter maior densidade de óxido na camada AAO, espessura uniforme e maior dureza, um novo processo de pré-tratamento foi desenvolvido.
O novo pré-tratamento por imersão em solução ácida tem a propriedade de reduzir as zonas pesadas intermetálicas de silício na superfície das peças. Esse novo processo patenteado, especialmente formulado com ácidos, foi aplicado às peças por 10 minutos a 90º C, resultando na distribuição mais uniforme do silício sobre a superfície do alumínio.
Esse tipo de condição superficial, após o pré-tratamento desenvolvido, resulta em uma adequada anodização do alumínio, como mostrado nas Figuras 3a) e 3b).
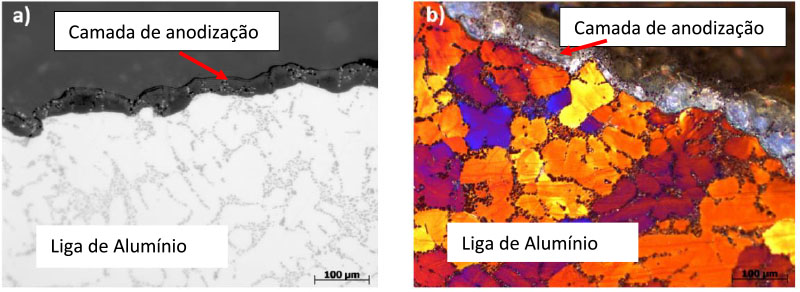
Esse aumento na uniformidade da distribuição de silício é resultado da diminuição de seu tamanho e forma, que permite uma maneira mais homogênea e com uma taxa de formação mais rápida ao processo de anodização. O resultado geral é um aumento de 30 a 40% na espessura da camada de óxido em comparação com o padrão de referência em condições operacionais iguais. Um resultado tão denso e homogêneo da camada AAO permite uma resistência mais elevada contra a corrosão, assim como à descoloração.
Melhorando ainda mais as propriedades da camada AAO, o próximo passo foi otimizar o eletrólito anodizante. A diferença do uso de aditivos à base de ácido oxálico, utilizados em soluções à base de ácido sulfúrico, com o uso do desenvolvimento de novos aditivos de base orgânica associados ao eletrólito anodizante é que estes agem para superar o efeito negativo dos intermetálicos do silício nas características do AAO. Eles ajudam a controlar a dissolução do alumínio e funcionam para incorporar o silício na camada de óxido com um mínimo impacto negativo na qualidade da camada de revestimento. Seu uso aumenta a condutividade do eletrólito e o calor gerado durante a formação da camada de anodização pode ser removido com mais eficiência da interface metal-eletrólito, aumentando a eficiência das reações de oxidação.
Ao incorporar o uso de uma mistura patenteada de aditivos orgânicos no eletrólito anodizante, os efeitos negativos das espécies intermetálicas de silício são suprimidos. A camada AAO resultante possui densidade aprimorada e um filme de óxido presente mais espesso, como mostrado nas Figuras 4b) em comparação com a anodização GSX, padrão apresentado na Figura 4a), referenciadas na figura 2.
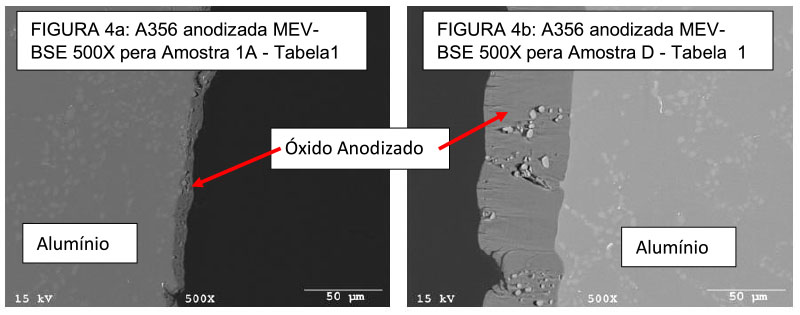
O desempenho geral e o sucesso da sequência aprimorada usando o pacote especial de pré-tratamento e aditivo orgânico ao eletrólito anodizante para criar a camada ideal de óxido foram facilmente avaliados através de testes laboratoriais de NSS.
O resultado após 800 hs de NSS
Os processos da TABELA 1 foram realizados para quatro sequências que são referenciadas na Figura 5. Essas amostras, A, B, C e D, foram processadas de acordo a demostrar as melhorias no desempenho de resistência contra a corrosão e a resistência à descoloração do alumínio fundido A356 anodizado.
O processamento adicional dessas superfícies anodizadas, através de um sistema orgânico de tingimento preto, foi concluído para as amostras B, C e D para ajudar a ver mais claramente a formação precoce de pontos de corrosão do alumínio. Além disso, a resistência à descoloração da superfície também é um indicador do desempenho da camada AAO em relação à resistência à corrosão.
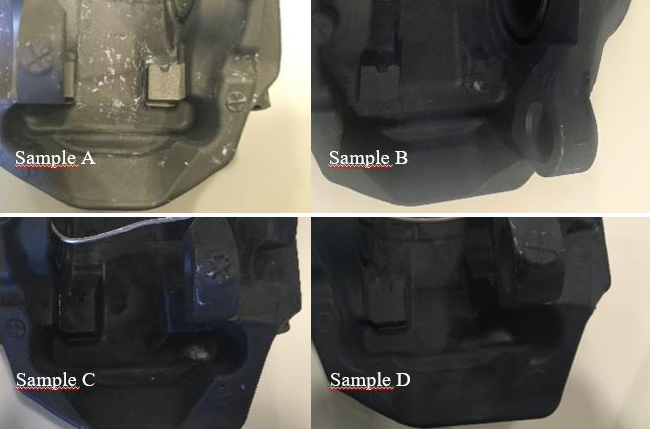
Todos foram avaliados após 800 horas de exposição ao Teste NSS. Conforme mostrado na Amostra A, há corrosão do metal base e são observadas algumas alterações de cor. De acordo com as imagens MEV, o melhor comportamento da corrosão foi obtido para as Amostras C e D, com a incorporação do pré-tratamento especial e o uso do aditivo orgânico no eletrólito anodizante.
Para a Amostra B, a demonstração da ação do aditivo orgânico na solução de anodização não mostra corrosão, mas a presença da alteração da cor da superfície indica a importância da espessura do filme de óxido para a integridade da cor.
Em muitas aplicações para anodização de ligas de alumínio fundido, a retenção e a estabilidade da cor, enquanto expostas a muitos fatores ambientais, é tão crítica quanto à resistência à corrosão. Ao incorporar o uso desses aditivos orgânicos no processo de anodização sulfúrica, e utilizando o processo especial de pré-tratamento, a homogeneidade e a espessura da camada de óxido podem ser melhoradas para ligas de alumínio fundido com maior teor de silício. Isso também fornece resistência à corrosão e à capacidade de obtenção de uma gama maior de possibilidades de cores, como mostrado na Figura 6, que tem maior resiliência contra a descoloração da superfície tingida ao longo do tempo em uso.
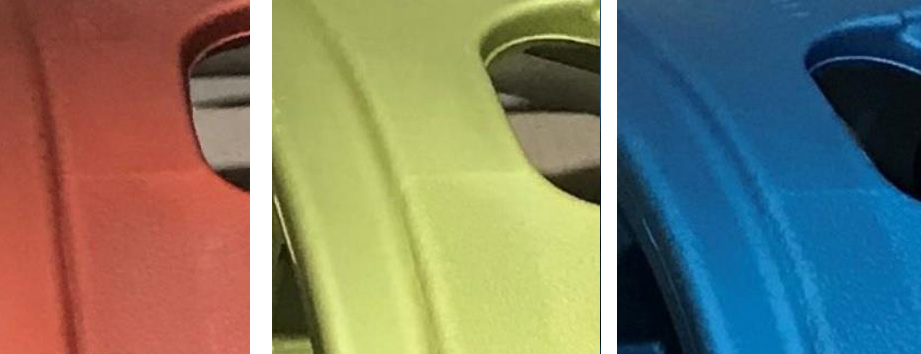
* Referências para artigos estão disponíveis mediante solicitação aos autores.