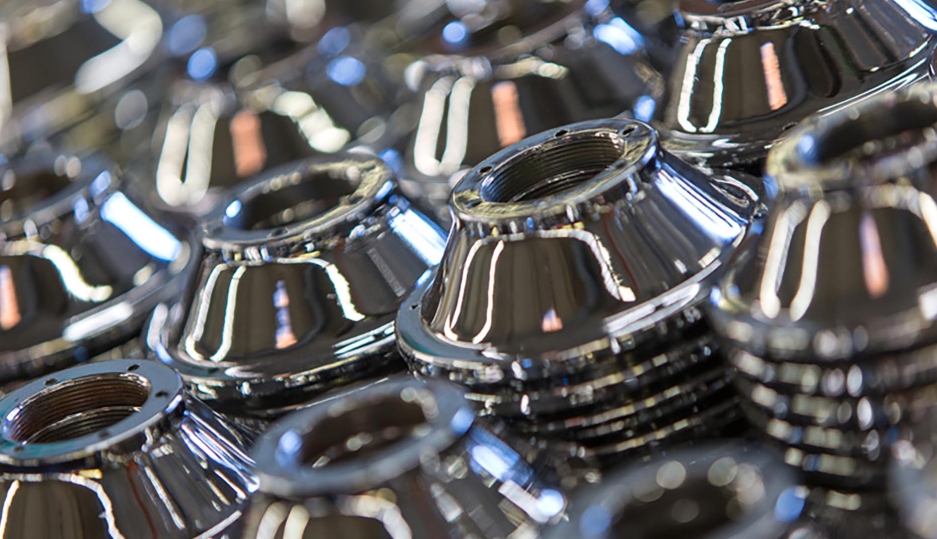
A evolução dos selantes como protetivo nas peças zincadas e a utilização como um produto de melhor controle do coeficiente de atrito
José Carlos D’amaro
Diretor de processos químicos da Alpha Galvano
jose.carlos@alphagalvano.com.br
Nos processos de tratamento de superfície, a preparação da base do substrato é um dos fatores mais importantes, pois irá interferir diretamente no resultado final. Ótimos processos para proteção contra a corrosão podem falhar por deficiência na limpeza, desengraxe ou decapagem da superfície.
Peças tratadas para melhorar a resistência à corrosão podem não atingir as expectativas ou as especificações simplesmente porque a base não foi bem preparada. Acabamentos decorativos de alta qualidade, com certeza, não serão obtidos sem uma boa preparação; no entanto, muitas vezes esse ponto é negligenciado ou não se dá a ele toda a atenção devida.
Historicamente, a mudança do comportamento do mercado foi necessária quando, há algumas décadas, houve a decisão de eliminar o cromo hexavalente devido aos problemas ambientais e à saúde operacional.
As primeiras tentativas de substituição foram utilizando processos base vanádio, molibdato, silanos e titânio; porém, nenhum conseguiu atender às necessidades que esses acabamentos exigiam. A melhor saída encontrada foi com a utilização dos passivadores base cromo trivalente que, entretanto, não conseguiam atender a todas as necessidades.
A resistência a corrosão no início era muito inferior aos processos hexavalente, além de que os cromatizantes hexavalente têm a propriedade auto cicatrizante: a película formada é um gel, qualquer agressão que provoque risco na superfície, a película gelatinosa se fecha e recobre o risco, enquanto isto não acontece com os processos com passivadores trivalente.
A solução encontrada para solucionar o problema foi selar a camada aplicando um selante, base silicato de sódio, que reage na superfície preenchendo todos os espaços vazios com uma película de silicato que, quando seca, sela completamente o filme de passivação, melhorando muito a resistência à corrosão. Esses processos, porém, ainda não atendiam perfeitamente toda a necessidade.
O filme de passivação formado era de camada muito fina, cerca de 40 a 50 nanômetros, com baixa resistência à corrosão, e o filme de selante, embora duro com a propriedade de ótima resistência à temperatura, resultava em coeficiente de atrito muito variado, causando problemas na hora do aperto dos parafusos e prisioneiros, no momento da montagem.
Na continuidade, uma das melhorias desse processo foi a introdução no mercado de produtos base silicato de lítio como substituto do sódio ou potássio, aumentando um pouco a resistência à corrosão; porém, continuava o problema de um coeficiente de atrito muito variado, tendo a necessidade de desenvolvimento de outros tipos de selantes para atender a essa propriedade.
Houve também a evolução dos passivadores com o surgimento do passivador trivalente de alta camada, conseguindo camadas de espessura até 400 nanômetros, cerca de 10 vezes aquela dos passivadores originais, com grande aumento na resistência à corrosão, ultrapassando as conseguidas com cromatizantes hexavalente. Atualmente, muitas especificações que exigem resistência à corrosão, principalmente peças automotivas, já são especificadas apenas com a utilização desses passivadores de alta camada.
Melhor controle de coeficiente de atrito
Para fixadores e parafusos ainda continuava a necessidade de um melhor controle do coeficiente de atrito, sendo necessário o desenvolvimento de processos para atender às especificações. Surgem, então, novas alternativas de selantes com inúmeras variações de tecnologia. Processos base emulsões de polipropileno, polietileno, ceras, compostos de acrilatos, acrílicos solúveis, emulsões acrílicas. Muitos processos também agregaram partículas de produtos de silício, que auxiliavam na resistência à corrosão, mas causavam variação no coeficiente de atrito.
Com o surgimento da nanotecnologia foram desenvolvidos produtos contendo nanopartículas de compostos de silício, que auxiliam na melhoria da resistência à corrosão e, dependendo das concentrações utilizadas, podem auxiliar no controle de coeficiente de atrito para atingir um determinado valor especificado.
O processo de selante significa aplicar uma fina camada de material orgânico, inorgânico ou mistura orgânico e inorgânico, com espessura de 0,5 a 2 µm (microns), dependendo do tipo aplicado, para modificar a resistência à corrosão, resistência química, e a superfície em relação a lubricidade e natureza hidrofóbica. Normalmente são aplicados imediatamente na sequência da linha de zincagem sobre o passivador, com a camada ainda fresca e ativa, formando uma camada composta.
Dependendo do tipo de passivação e selante aplicado, a resistência à corrosão na câmara de salt spray pode variar desde 48 horas até acima de 500 horas sem a formação de corrosão branca.
Conclusão
Os passivadores trivalentes e selantes foram desenvolvidos como alternativa para a substituição dos processos de cromatizantes hexavalentes – inicialmente com muitas restrições e muita desconfiança, com processos que resultavam em camada muito fina e baixa resistência à corrosão.
Na tentativa inicial da utilização de selantes base silicatos foi-se atendendo parcialmente as necessidades de resistência à corrosão, com um filme duro e resistente que, em algumas aplicações, traziam grandes vantagens, porém, em outras (por exemplo, onde necessitava-se de um melhor controle de atrito) o resultado não era satisfatório, não devendo ser utilizado em peças que sofreram deformação ou pintura.
Muitas novas tecnologias foram, então, desenvolvidas, desde a utilização de ceras, como emulsões de polietileno, polipropileno, acrilatos, até soluções de acrílico. Em seguida, a adição de produtos com partículas de compostos de silício a essas misturas orgânicas, obtiveram excelentes resultados de proteção.
Com o surgimento das tecnologias de nanopartículas, as partículas de compostos de silício foram substituídas por nanopartículas, com melhoria no controle do coeficiente de atrito.
Os passivadores também tiveram uma ótima evolução, com o desenvolvimento de processos que resultam em camadas até 10 vezes maiores que as iniciais, atingindo camadas de passivação superiores a 400 nanômetros.
Normalmente, essas tecnologias não são aplicadas individualmente. Os processos são formulados otimizando as misturas para diferentes aplicações.
Para atender as especificações, pode-se criar um mix para atingir resultados de salt spray, desde 48 até superiores a 500 horas, sobre camadas de zinco eletrodepositadas. Enquanto no controle de atrito, também são possíveis produtos que podem atender especificações de coeficientes de atrito de 0,08 + 0,03, até superiores a 0,30 + 0,03, que são as faixas de especificações encontradas no mercado, dependendo da aplicação.
EXEMPLOS TÍPICOS DE SELANTES E TOP COATS
Inorgânicos, base silicatos |
Mais simples e econômicos. Selantes de uso geral. Filme duro, boa resistência à corrosão, mas não adequado para peças que sofrem deformação ou pintura posterior. |
Selante orgânico base acrílico |
Filme brilhante, alta resistência à corrosão, econômico. Pode ser utilizado em diversas concentrações para a obtenção de filmes mais ou menos espessos, dependendo da aplicação, usado em alguns casos como ajustador de coeficiente de atrito com alto valor, acima de 0,20 + 0,03. |
Selante orgânico, polímeros e ceras |
Acabamento com excelente brilho, proteção contra a corrosão e com as misturas ajustadas para conseguir baixos e controlados coeficientes de atrito. |
Selante orgânico/inorgânico |
Acabamento com bom brilho, ótima proteção contra a corrosão, com misturas ajustadas para se conseguir coeficientes de atrito adequados para as especificações intermediárias. |