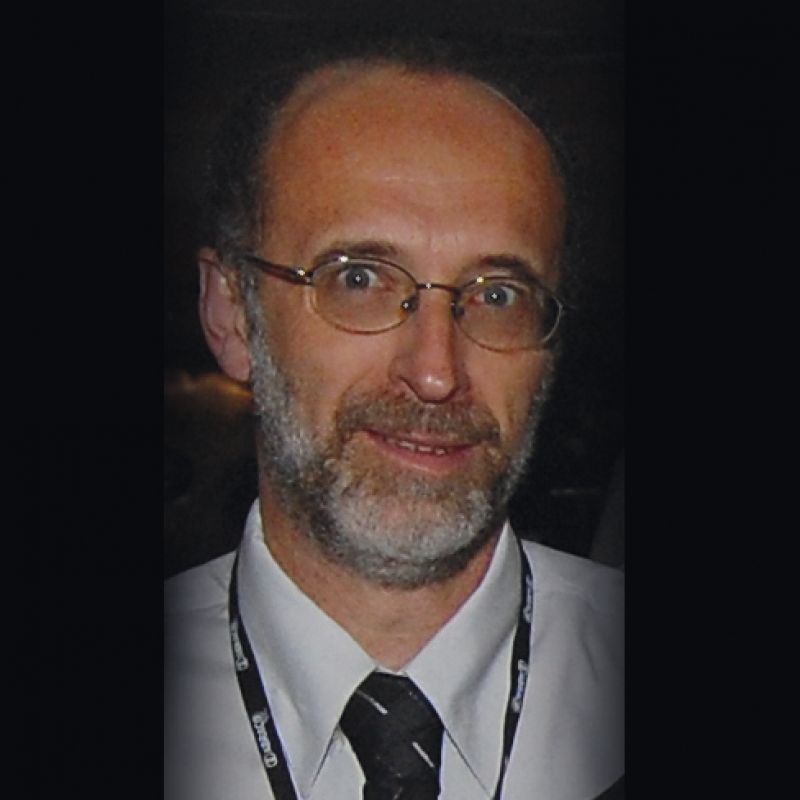
Como aumentar a vida útil dos componentes dos equipamentos pelos revestimentos que podem ser aplicados em diversos processos de metalização, reduzindo custos e otimizando operações
Abstract
According to the 2018 Brazilian Mineral Yearbook with data from 2017, Brazil is one of the five largest mineral producers in the world, concentrating around 80% of its production in metallic minerals, the main ones being a total of 95, 6% are: iron with 71.1%, copper with 9.4%, gold with 8.9%, aluminum with 3.7% and nickel with 2.5%. Among the sector’s challenges are the reduction of environmental impacts, the use of sustainable resources, the increase in activity security and the increase in productivity. And it is there, in these first and last challenges, that the metallization (thermal spray) processes have been acting progressively, helping in the search for the reduction of the environmental impact and losses in productivity, thus obtaining improvement in the environment and in the performance of each stage of its production. Mainly acting to mitigate the effects of wear, which causes the removal of physical material and the corrosion that causes chemical degradation, the appropriate coatings are applied through metallization equipment of different types, thus optimizing the use of numerous parts, parts and equipment used in the mining sector.
Resumo
Segundo o Anuário Mineral Brasileiro de 2018, com dados de 2017, o Brasil é um dos cinco maiores produtores minerais do mundo, concentrando cerca de 80% de sua produção em minerais metálicos, sendo que os principais deles, num total de 95%, 6% são: ferro, com 71,1%; cobre, com 9,4%; ouro, com 8,9%; alumínio, com 3,7%; e níquel, com 2,5%. Dentre os desafios do setor, constam a redução de impactos ambientais, o uso de recursos sustentáveis, o aumento de segurança da atividade e a elevação da produtividade. E são no primeiro e último desafio que os processos de metalização (aspersão térmica) têm atuado de forma progressiva, ajudando na busca da redução do impacto ambiental e de perdas na produtividade, obtendo, assim, melhoria no meio-ambiente e no desempenho de cada etapa de sua produção. Principalmente atuando de forma a mitigar os efeitos do desgaste, causador da remoção de material físico e da corrosão causadora da degradação química, os revestimentos adequados são aplicados através de equipamentos de metalização de diferentes tipos, otimizando, assim, a utilização de inúmeras partes, peças e equipamentos utilizados no setor da mineração.
1. INTRODUÇÃO
1.a. A mineração e o tamanho do seu mercado no Brasil
O Brasil, como um dos cinco maiores produtores minerais do mundo, conta com mais de 3.000 minas ao longo de seu território. A mineração, como um todo, participou com 4,69% do PIB (Produto Interno Bruto), entre as riquezas geradas no país. “Em 10 anos, o desenvolvimento da extração mineral foi de 550% no país” (7.a.). Na época, o Anuário Mineral Brasileiro de 2018, com dados de 2017, apontava o setor mineral como responsável por 21% da balança comercial, com US$ 49,7 bilhões de vendas ao exterior contra US$ 26,4 bilhões de importações. Como um dos resultados dessa atividade, outros impactos na economia – como por exemplo a Compensação Financeira pela Exploração de Recursos Minerais (CFEM) –, o valor utilizado para custear a infraestrutura de municípios e regiões onde a atividade mineral ocorre –, ultrapassou R$ 1,5 bilhão.
Em relação a outros segmentos industriais, a mineração destaca-se como fornecedora de matéria-prima basicamente para o setor siderúrgico e metalúrgico, que a transforma em produtos de interesse para várias outras áreas. Indiretamente, atua na indústria como um todo: no setor automobilístico, construção civil, máquinas industriais, transportes por tubulações, embalagens, etc. Quanto à geração de empregos em 2017, destacou-se com 733 mil empregos diretos e mais de 2,2 milhões de empregos indiretos.
1.b. Os atuais desafios da mineração no Brasil e no mundo
A redução de impactos ambientais gerada pelas atividades do setor de mineração, da fase de extração à fase de beneficiamento e ao respectivo descarte, além de necessária, influi diretamente no meio ambiente. Destaca-se, em seu processo produtivo, um grande consumo de água e energia elétrica e a utilização dos recursos naturais, por exemplo, nas fases de britagem, aglomeração e beneficiamento do minério que, caso otimizadas em suas operações, resultam em diminuição dos impactos negativos causados à natureza e na melhoria da eficiência do uso dos recursos naturais. Ou seja:
• A utilização dos recursos sustentáveis, onde a busca por novos métodos que, por exemplo, não utilizem água ou gerem menos contaminantes é essencial;
• O aumento de segurança, tanto em relação aos colaboradores quanto ao meio-ambiente, monitorando barragens e modificando a forma atual de tratamento de resíduos;
• A elevação da produtividade, sem afetar a segurança e a sustentabilidade, com base em pesquisas e desenvolvimento, objetivando a redução de perdas e a otimização do processo, de forma cumulativa em cada uma de suas fases.
1.c. A metalização propondo soluções no segmento de mineração
Graças à extensa gama de materiais disponíveis para revestimentos é possível, através dos processos de metalização, criar alternativas voltadas a solucionar os principais problemas na mineração em relação ao elevado nível de degradação sofrido pelos seus equipamentos quando em operação – principalmente, o desgaste e a corrosão, quer ocorram de forma individual ou combinadas entre si, como por exemplo, em altas temperaturas.
2. POR QUE A METALIZAÇÃO?
2.a. O que é a metalização?
Segundo a AWS (American Welding Society), Aspersão Térmica (ou Metalização) é definida como: “Grupo de processos nos quais se divide finamente materiais metálicos e não metálicos que são depositados em uma condição fundida ou semifundida sobre um substrato preparado para formar um depósito aspergido”.
2.b. Quais as vantagens dos processos de metalização?
Conhecido como um grupo de processos que mantém a integridade do metal-base, não o deformando e nem alterando a sua composição química ou estrutura física durante a aplicação dos mais diversos tipos de materiais (exceto quando depositados materiais autofundentes), torna-se uma excelente solução multivalente para proteção, recuperação e ampliação da vida útil de peças, equipamentos e estruturas nos mais diversos segmentos industriais, inclusive no de mineração.
2.c. Os processos de metalização e processos complementares mais utilizados na mineração
Dependendo da situação de trabalho da peça ou do componente, um dentre os vários tipos de processos de metalização pode ser a melhor opção. Apesar desses equipamentos poderem trabalhar aplicando vários tipos de materiais, alguns deles são mais indicados em função de alguns materiais específicos. A saber:
2.c.1. Metalização à Chama (Flame Spray)
Entre os processos de metalização, é considerado o de maior versatilidade e o de menor custo em relação aos seus equipamentos. Opera através da combustão de gases para fusão, ou semifusão dos materiais, acelerando as partículas em direção à região a ser revestida, devidamente preparada. A matéria-prima pode ser utilizada na forma de pó, arame, barra ou cordão, e as temperaturas alcançadas no interior do equipamento são da ordem de 2.300°C, dependendo do tipo de equipamento usado. Os arames são metálicos (ferrosos, não-ferrosos e ligas especiais) – enquanto as demais formas de materiais, vão desde os metálicos (ferrosos, não-ferrosos, ligas especiais e autofundentes) até os polímeros e cerâmicos. No caso da aplicação de materiais autofundentes, as camadas sofrem refusão após aplicadas a temperaturas de cerca de 800°C. As velocidade atingidas pelas partículas são superiores a 80 m/s.
2.c.2. Metalização a Arco Elétrico (Arc Spray)
Bastante utilizada na deposição de metais ferrosos, não-ferrosos e ligas especiais, também pode depositar cermets, carbonetos, nitretos, etc., em núcleos revestidos na forma de arames, em superfícies devidamente preparadas. Utiliza energia elétrica como fonte de calor para a fusão dos materiais, alcançando temperaturas de arco formado entre dois arames, superiores a 25.000°C.
2.c.3. Metalização Oxicombustível de Alta Velocidade (High-Velocity Oxy-Fuel Spraying) (HVOF ou HP-HVOF) e Metalização Ar Combustível de Alta Velocidade (HVAF-High Velocity Air Fuel)
O HVOF utiliza como fonte de calor a combustão de gases, resultantes da mistura de oxigênio com um fluído combustível (gasoso ou líquido – querosene), gerando temperaturas de jato da ordem de 3.500 °C. Devido à sua geometria interna, as partículas chegam a alcançar velocidades supersônicas de até 1.000 m/s. Graças à essa velocidade, as partículas tendem a aglutinarem-se na forma de camadas com índices de porosidade inferiores a 1%, portanto, bem abaixo dos processos de metalização à chama e a arco elétrico – inferiores a 15%. O processo de metalização HVOF utiliza como seus principais revestimentos contra o desgaste abrasivo e erosivo, materiais à base de carboneto de tungstênio (WC) em matriz dúctil de cobalto (Co) e/ou cromo (Cr). Caso também ocorra oxidação, essa matriz dúctil pode ser, ou conter, níquel (Ni).
Um avanço obtido em relação ao processo HVOF foi o processo HVAF, no qual o ar é utilizado na combustão de um combustível líquido ao mesmo tempo em que resfria a tocha, diferentemente do HVOF, que utiliza água para o seu resfriamento.
2.c.4. Metalização à plasma (Plasma Spray)
A ionização dos gases gera calor através de arco não transferindo mais água de resfriamento. Enquanto o gás primário forma o plasma, o secundário fornece energia e velocidade às partículas, gerando temperaturas internas entre 12.000 °C e 25.000 °C, suficientes para a fusão de, por exemplo, materiais ferrosos, não-ferrosos, ligas especiais, carbetos, polímeros e especialmente os oxicerâmicos, sem, contudo, transmiti-la ao metal-base, não o deformando.
A deposição de materiais cerâmicos possui características de barreira térmica, resistência ao desgaste por erosão e abrasão, e isolamento do metal-base contra o ataque de produtos corrosivos. Entre outras características da metalização à plasma, temos “a formação de microestruturas com grãos finos não colunares e equiaxiais, capacidade de produção de revestimentos homogêneos que não sofrem alterações em função da espessura e da duração do tempo de deposição e a capacidade de processar materiais em praticamente qualquer ambiente (por exemplo, ar, gás inerte de pressão reduzida, alta pressão, sob água)” (7.b.). As velocidades atingidas pelas partículas giram em torno de 200 m/s a 800 m/s, e a densidade final da camada fica entre 90% e 99% (Foto 4).
2.c.5. Metalização a Frio (Cold Spray)
Com temperaturas mais baixas, em torno de 800 °C, limita-se atualmente à aplicação de materiais dúcteis, como alguns metais e ligas não ferrosas, algumas ligas especiais e metais-polímeros – onde os metais dúcteis estejam presentes em ao menos 50% da liga. As velocidades alcançadas pelas partículas vão de 300 m/s a 1.200 m/s devido à geometria interna de seu canhão. As baixas temperaturas envolvidas fazem com que as composições dos materiais se mantenham de maneira mais íntegra que os demais processos de metalização, enquanto que, devido à velocidade das partículas, a sua porosidade chega a alcançar índices inferiores a 0,5%.
2.c.6. Plasma de Arco Transferido (PTA Plasma Transferred Arc)
Processo de soldagem que, diferentemente dos processos de metalização, envolve a adesão metalúrgica da camada ao metal-base. É utilizado como processo complementar ao processo HVOF em recentes avanços em aplicações no setor de mineração, tendo como base a formação de dois arcos elétricos – um deles, não-transferido, que acelera o gás de plasma e permite a ignição do outro arco, o arco transferido.
O arco queimando com alta densidade de energia, entre o eletrodo e a peça, funde tanto o metal-base como o pó metálico utilizado como consumível, gerando, assim, o revestimento. O material utilizado em mineração no processo PTA complementar ao de metalização HVOF é o carboneto de tungstênio para proteção ao desgaste e à corrosão.
3. A METALIZAÇÃO NA PRODUÇÃO E MANUTENÇÃO DO SETOR MINERAL
3.a. A metalização utilizada em peças novas ou usadas na mineração
Prevendo o alto nível de degradação dos componentes dos equipamentos nas operações de mineração, acima ou abaixo da superfície, os processos de metalização podem ser utilizados tanto para prevenir a ação dos agentes de degradação como para recuperar tais componentes após a atuação desses agentes.
3.b. Alguns dos principais problemas operacionais da indústria de mineração
Como na maioria dos processos industriais, os fatores de máxima importância a serem levados em conta são o aumento da vida útil de peças e equipamentos e o aumento da produtividade. A otimização de peças e equipamentos, além de reduzir perdas, proporciona ganhos de produtividade. É óbvio que os equipamentos de mineração estão expostos a situações altamente agressivas durante as operações de escavação, remoção e transporte, tais como desgaste por abrasão, erosão e impacto, e por corrosão – causada pelo contato com rochas, lama, pó, água, variações de temperatura, etc.
4. A METALIZAÇÃO PROPONDO SOLUÇÕES NA INDÚSTRIA DA MINERAÇÃO
4.a. Como a metalização pode otimizar o funcionamento de peças e equipamentos na mineração
Os chamados revestimentos duros, revestimentos cerâmicos e revestimentos metálicos, aplicados através dos diversos processos de metalização, podem oferecer um amplo leque de soluções voltados à mineração, envolvendo barreiras térmicas, proteção contra o desgaste, inclusive por partículas abrasivas, proteção contra a corrosão, proteção em ambientes a altas temperaturas, e recuperação dimensional.
4.b. Partes, peças e equipamentos da mineração que podem ser protegidos ou recuperados pela metalização
Máquinas, equipamentos e componentes, quer de mineração subterrânea ou de superfície, expostas a severas condições de trabalho, que podem ser protegidos ou recuperados pela metalização são, por exemplo: autoclaves, barris de armazenamento, bombas de lama, bondes, britadores, caixas de engrenagens, caixas de engrenagens cônicas, caixas de rolamentos, caminhões de transporte, carregadeiras de perfuração, cortadores automáticos de carvão, escavadeiras, estatores, esteiras de transporte, filtros, ferramentas de perfuração, furadeiras, linhas de rejeitos, mancais, misturadores, moinhos, motores hidráulicos, pás carregadeiras, pás de escavação, perfuratrizes, reatores, reatores ácidos, rodas, rotores, tanques de lixiviação, torrefadores, tratores, tremonhas, trituradores, trommels, ventiladores, etc. E ainda: agitadores de filtro, assentos de rolamentos, baldes, buchas de bombas, carcaças de bombas, coroas de cubos de roda, discos e lâminas agitadoras de autoclave, eixos da cabeça de transmissão principal dos ríperes de cortadores automáticos de carvão, eixos de saída, engrenagens de acionamento, flanges de acionamentos, hastes de cilindro hidráulico, hastes do pistão do cilindro em arco, lâminas de reatores ácidos, mandris, martelos de esmagamento, parafusos de escavadeiras, pontas de britagem, pistões de motor hidráulico, pistões dos conjuntos de macacos traseiros, pistões de bomba, placas de apoio de bombas de lama, polias estriadas, porta-rolamentos, raspadores, rolos classificadores, sedes de vedação, suportes dianteiros de suspensão e fusos de rodas de caminhões de mineração, roscas de alimentação, suportes hidráulicos de poço, telas, travas e dentes de pás de escavação, válvulas-esfera, entre outros.
4.c. A metalização revestindo peças novas ou usadas na mineração
São várias as aplicações de revestimentos depositados pelos processos de metalização voltados ao segmento de mineração; exemplos:
• Revestimentos de rolos classificadores de pelota crua por metalização a arco elétrico, bem como alumínio e aço inox para proteção contra a corrosão;
• Revestimento de metal patente em mancais por metalização à chama (Foto 1);
• Revestimentos autofundentes aplicados por metalização à chama em buchas de bombas, agitadores de filtro, roscas de alimentação, pistões de bomba e raspadores;
• Carcaças de bombas com diâmetros internos revestidos com WC por HVOF (Foto 2);
• Parafusos de escavadeiras para materiais abrasivos, peças de desgaste para ferramentas de misturadores, e ferramentas de perfuração protegidas, através da aplicação, com equipamentos de metalização à chama com posterior fusão de camadas formadas por WC e matriz de NiCrBSi (7.c.) (7.d.);
• Hélices de misturadores revestidas com Al2O3/Ti através de equipamento de metalização à chama otimizado, com resultados próximos aos obtidos nas camadas aplicadas por metalização à plasma (7.c.);
• Utilização de camadas de óxido de cromo aplicadas por metalização à plasma, e de carbeto de tungstênio por metalização hipersônica (HVOF) (7.e.);
• Recuperação de suportes dianteiros de suspensão e fusos de rodas de caminhões de mineração utilizando equipamento HVOF;
• Eixos da cabeça de transmissão principal dos ríperes de cortadores automáticos de carvão, recuperados com a utilização de equipamento de metalização a arco elétrico, aplicando aço inox com alto teor de cromo, resistente a desgaste e à corrosão;
• Segundo estudos realizados (7.f.), o revestimento de WC com matriz de Ni aplicado pelo processo HVOF, em lâminas de um reator ácido, faz com que o componente resista ao ataque do ácido sulfúrico, com 90% de pureza, a temperaturas superiores a 200 °C. Dessa forma, a vida útil das lâminas do agitador foi ampliada de 9 para 50 meses;
• Componentes de mineradoras, como pistão do conjunto do macaco traseiro, pistão do motor hidráulico, haste do pistão do cilindro em arco, e suporte hidráulico de poço, recuperados com aplicação de aço inox com alto teor de cromo, bem como, placa de apoio de bomba com deposição do mesmo material através do processo HVAF (7.g.);
• Discos e lâminas agitadoras de autoclave de titânio, em mineração de ouro, expostas a uma pasta de ácido sulfúrico a 1,8 %, a uma temperatura de 218 °C, sem revestimento, possuíam uma vida útil de 9 meses, já revestidas com titânio por metalização tiveram a sua vida útil ampliada para 50 meses (7.h.).
Foto 1 - Metalização à chama com metal patente em mancal
Foto 2 - Metalização com WC por HVOF em carcaça de bomba
Foto 3 - Hélice de misturador revestida com Al2O3/Ti
Foto 4 - Equipamento de metalização à plasma para colocar equipamento de metalização à chama otimizado - deposição de vários materiais, especialmente cerâmicos
5. OS AVANÇOS DA METALIZAÇÃO EM APLICAÇÕES NA INDÚSTRIA DE MINERAÇÃO
5.a. A nanotecnologia na metalização em serviços severos da mineração
Estudos realizados, em 2000 (7.i.), para melhoria de revestimentos cerâmicos aplicados em válvulas de-esfera para lixiviação ácida de alta pressão (HPAL-High Pressure Acid Leach), compararam revestimentos cerâmicos utilizando matéria-prima em forma de pó convencional à base de Cr2O3 e revestimentos em pó nanoestruturados à base de TiO2 – ambos aplicados através do Processo de Metalização à Plasma a Ar (APS-Air Plasma Spraying). Essas válvulas, utilizadas em situações severas, para conter e controlar o fluxo de lama ácida quente, operam sob altas temperaturas (até 265 °C), altas pressões (até 798 psi), altas concentrações de ácidos (> 95% H2SO4), e altas concentrações de sólidos (> 20% em peso). O resultado da camada nanoestruturada (base TiO2) mostrou-se superior após testes comparativos, uma vez que a esfera em operação apresentou apenas algumas regiões isoladas sem revestimento devido à corrosão, desgaste abrasivo e erosivo em contraste com a esfera que recebeu camada convencional (base Cr2O3), que apresentou, sob as mesmas condições, grandes regiões sem revestimento.
5.b. Otimizando os processos de metalização na mineração
5.b.1. Melhorando a refusão das camadas aplicadas
Visando otimizar a durabilidade do conjunto camada-substrato no segmento de mineração, estudos (7.j.) foram realizados visando refundir camadas de metal duro aplicadas sobre compósitos de matriz de aço, densificando-as e aumentando a sua resistência de ligação ao metal-base através da utilização de uma fonte de aquecimento infravermelho de alto fluxo, melhorando, assim, o desempenho de revestimentos aplicados por metalização em algumas peças críticas na indústria da mineração. Como benefício, obtém-se redução de perdas por atrito, mantendo-se a forma ideal da peça, reduzindo o tempo de inatividade do equipamento e duplicando a vida útil dos componentes de desgaste.
5.b.2. Agregando processos
Em situações extremas de desgaste e corrosão na indústria de mineração – como, por exemplo, na movimentação de areias betuminosas –, estão sendo utilizados, cada vez mais, revestimentos aplicados por metalização HVOF, seguidos por sobreposições aplicadas por PTA. Essa sobreposição, quando possível, chega a duplicar a vida útil das peças quando comparada a simples deposição por HVOF.
6. CONCLUSÃO
Utilizando uma vasta gama de alternativas de processos e materiais, a metalização por aspersão térmica atua no setor de mineração através da aplicação de camadas protetivas, com os mais diversos objetivos, de forma a reduzir os prejuízos causados pela severidade de suas operações, que sejam acima ou abaixo da superfície. Além dos processos convencionais e suas respectivas formas de utilização, avanços são buscados de forma contínua, visando otimizar os resultados protetivos das camadas aplicadas, quer seja atuando nas diversas formas de desgaste sofridas pelos vários tipos de componentes dos equipamentos de mineração, bem como da atuação, também severa, da corrosão, principalmente quando combinada com a ação de altas temperaturas. Sendo assim, a vida útil dos componentes dos equipamentos ligados ao setor de mineração é ampliada através das várias possibilidades de revestimentos que podem ser aplicados pelos diferentes processos de metalização e, consequentemente, otimizando suas operações, reduzindo, assim, seus respectivos custos.
BIBLIOGRAFIA
7.a. Indústria de Mineração no Brasil e seu Crescimento - Website Metso Brasil - https://www.metso.com/br/blog/mineracao/crescimento-da-mineracao-no-brasil/ (visualizado em 19/02/2021)
7.b. Processing And Characterization of Plasma Spray Coatings of Industrial Waste and Low Grade Ore Mineral on Metal Substrates by Ajit Behera - National Institute of Technology, Rourkela, India, May, 2012
7.c. Revestimentos Duros Aplicados por Aspersão Térmica (Metalização) Top Jet/Master Jet - Saint-Gobain Solutions - Saint-Gobain do Brasil Produtos Industriais e para Construção Ltda. - Divisão Materiais Cerâmicos - Ceramic Materials/ HPM-Brazil - Demais informações: Website Saint-Gobain - https://www.ceramicsrefractories.saint-gobain.com/markets/metallurgy-mining-mineral-processing (visualizado em 23/02/2021)
7.d. Aspersão Térmica - Flexicord - Catálogo 2017 - Saint-Gobain Solutions - Saint-Gobain do Brasil Produtos Industriais e para Construção Ltda. - Divisão Materiais Cerâmicos - Ceramic Materials/HPM-Brazil - Demais informações: Website Saint-Gobain - https://www.ceramicsrefractories.saint-gobain.com/markets/metallurgy-mining-mineral-processing (visualizado em 23/02/2021)
7.e. Citação de Thiago Coelho - Rede Social Linkedin em 04/10/2020
7.f. Thermaspray - Coating Solutions Partner for the Mining Industry - Press Release - 23 January 2018 - Website Thermalspray - https://www.thermaspray.co.za/downloads.html#industries (visualizado em 05/02/20210)
7.g. Salvage & Restoration Industry-Mining - Website MSSA Metal Spray Supplies Australia - https://metalspraysupplies.com/metal-spray-industry-applications/salvage-restoration?start=1 (visualizado em 17/02/2021)
7.h. Gold Mine Autoclave-Agitator Blades - Watson Rinding and MFG. - Website Watson Rinding http://www.watsongrinding.com/media/downloadable-brochures-and-specs/ (visualizado em 21/02/2021)
7.i. FW Gartner Develops a Successful Thermal Sprayed Nanostructured Coating for Severe-Service Mining Application by George Kim - Spraytime - Volume 13, Number 1, First Quarter 2006, May 15-18, 2006
7.j. Metal-matrix Composites and Thermal Spray Coatings for Mining Machines - Minnig Project Fact Sheet - June 2001 - Office of Industrial Technologies Energy Efficiency and Renewable Energy U.S. Department of Energy Washington, D.C. 20585 - Office of Industrial Technologies Clearinghouse
7.k. Mining Sector: Metal Coating and Wear Resistence - Website Métallitech https://metallitech.qc.ca/en/thermal-srpay-mining/ (visualizado em 17/02/2021)
7.l. Analysis of Thermal Spraying in the Industries of Western Canada by André G. MacDonald, Ph.D., P.Eng.
7.m. Development of Advanced Surface Enhancement Technology for Decreasing Wear and Corrosion of Equipment
Used for Mineral Processing by Daniel Tao, R. Honaker, B.K. Parekh (Department of Mining Engineering, University of Kentucky) and Craig A. Blue, Narendra B. Dahotre (Oak Ridge National Laboratory) - Prepared for U.S. Department of Energy Mining Industry of the Future Program - December, 2007
7.n. Thermal Spraying & PTA - Website Voestalpine https://www.voestalpine.com/welding/Brands/UTP-Maintenance/Thermal-Spraying-PTA (visualizado em 21/02/2021)
7.o. Mining-Thermal Spray Coating - Website A&A Coatings https://www.thermalspray.com/industries/mining/ (visualizado em 21/02/2021)
7.p. Product/Service Information-Mining Industry Coatings-Coating Design and Manufacturing - Website NTST http://www.nevadathermalspray.com/ (visualizado em 05/02/2021)
7.q. A Metalização por Aspersão Térmica e o Seu Universo de Aplicações - Luiz Cláudio O. Couto - Revista: Tratamento de Superfície/ABTS Nº 219-Abril 2020
7.r. Cursos de Metalização/Aspersão Térmica Luiz Cláudio O. Couto - Faculdades Oswaldo Cruz e ABM (Associação Brasileira de Metalurgia, Materiais e Mineração - 2013 a 2020
7.s. Fotos 1 e 2 gentilmente cedidas pela Revex Brasil Ltda.
7.t. Fotos 3 e 4 gentilmente cedidas pela Saint-Gobain Coating Solutions