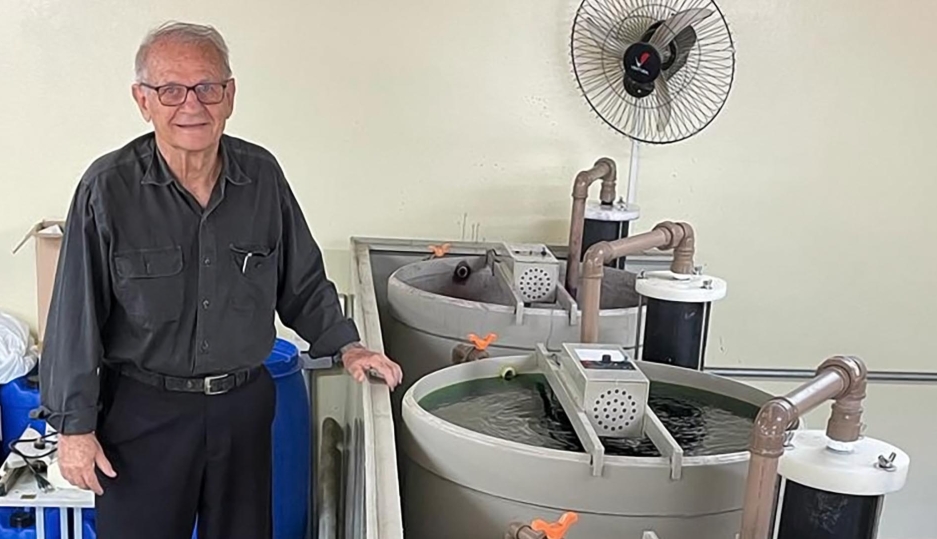
Hanns Langer dedicou mais de seis décadas à galvanoplastia, onde ainda atua como consultor
Os mais de 60 anos de atuação de Hanns Langer no setor de galvanoplastia. “O maior aprendizado foi que todo dia que passa, você aprende algo novo colocando a ‘barriga no tanque’”
Quando tinha 9 anos, Hanns Langer já tinha familiaridade com processos de tratamento de superfície, seu pai trabalhava no setor de rotogravura, cobreamento, gravação e cromaçao de cilindros para impressão e o processo o encantava. ”Meu pai me contaminou com os processos de galvanoplastia, e me ‘viciou’ até hoje”, conta o profissional; desde então são mais de seis décadas de atuação em tratamento de superfície.
Tudo começou na Alemanha: “No último ano da Segunda Guerra Mundial, nasci em Leipzig, Alemanha, em 26/09/1945. Em 1950, meu pai recebeu convite do Sr. Assis Chateaubriand para trabalhar no Rio de Janeiro, na revista ‘O Cruzeiro’, do grupo Diários Associados, no setor de rotogravura – antes da guerra meu pai trabalhava na empresa Giesecke & Devrient, que imprimia cédulas de papel moeda para a Alemanha e a Espanha. Ele veio sozinho para o Rio, com um voo que levou 24 horas na época. Após se estabelecer, um ano depois, viemos nos juntar a ele. Viemos de navio, que levou 14 dias para chegar, em 23/09/1951. No RJ, estudei na escola alemã Cruzeiro, de 1952 até 1953. Meu pai se transferiu para São Paulo no fim daquele ano, pois o campo de trabalho era maior. Ele trabalhava no setor gráfico de rotogravura, onde os cilindros eram cobreados, gravados e cromados, e quando eu tinha 9 anos, em 1954, ia visitá-lo e ele me explicava que o cobre do anodo ia para o cilindro; eu ficava encantado com a cor do banho de cobre ácido com um azul muito bonito. Em São Paulo, estudei no Colégio Porto Seguro, de 1954 até 1964, me formei na escola secundária em línguas modernas, em 1965”.
Quando tinha 14 anos, Hanns começou a trabalhar no setor, com o pai, que havia fundado a SETECOBEL – Serviços Técnicos de Cobre Eletrolítico. “Comecei, primeiramente, purificando cobre por eletrólise, para serem usados como anodos com 99,99 % de pureza. Depois, a firma mudou para um prédio maior, onde, além de cobreação de cilindros para impressão, montamos uma cromação com polimento. Comecei inicialmente como polidor, depois passei para a linha de Cu, Ni e Cr. Em 1970, a firma foi vendida e passou a se chamar Huzicromo”, conta.
Langer: “A Indústria não seria viável sem o setor de tratamento de superfícies”
Fluente em alemão, o executivo foi para a Europa, em 1966, para terminar a sua educação a pedido de seu pai, ele detalha: “Como a galvanoplastia é um ramo da química, uma combinação de várias áreas de estudo, como Eletroquímica, Mecânica, Elétrica, Química e Eletrônica, o meu querido pai, me mandou estudar na Alemanha, pois era um dos poucos países que tinham bons cursos de galvânica naquela época dos anos de 1960”. Em Berlim, Langer fez Administração de Empresas e ampliou os estudos realizando Engenharia Operacional (TS e Metalurgia), além de consolidar os conhecimentos em tratamentos superficiais, fazendo também a Escola Técnica de Galvanoplastia, local onde se formou em Galvanotécnica.
Após esse período, retorna ao Brasil, em 1971, mas volta ao país europeu pouco tempo depois, ele conta: “Meu pai tinha acabado de vender a firma e não pude mais atuar nela, então retornei para a Alemanha e fiz estágio na firma Kiesow de Detmold, para fundar uma filial para o Brasil, mas que não mostrou interesse em continuar os negócios por aqui, após um breve período. Voltei novamente para a Alemanha, de 1972 a 1975, para trabalhar em uma firma de fabricação de equipamentos galvânicos e gráficos na G.W Mettenheimer, em Dörnigheim, perto de Frankfurt, onde fui montador e instrutor em vários continentes dos equipamentos galvânicos e gráficos”.
Uma situação muda tudo
Em 1975 retornou ao Brasil para acompanhar o pai que havia sofrido “grave traumatismo craniano ao ser assaltado, fato que o afetou para o resto de sua vida”. A partir dali o profissional se estabeleceu por definitivo no país, contando com consultorias e trabalhos pontuais no exterior. “Trabalhei na La Fonte, em 1976, por 1 ano, depois indo para a firma Cascadura - Cromo Duro e Metalização por Aspersão Térmica, de 1977 até 1982; de 1980 até 1982 trabalhei como Gerente de Revestimento Técnico para a agregada da Cascadura, que depois passou a chamar STA Säkaphen, filial da Säkaphen alemã. Fiz serviço de revestimentos em tanques da Polisul, no RS, com revestimentos especiais, que eram aplicados em misturadores gigantes, de diâmetro 4,5m x 64m, para pó de polietileno. Como também revestimento interno de tubos de trocadores de calor de, aproximadamente, 20 t. O maior desafio no cromo duro foi revestir com mais de 300 microns em uma das maiores peças de diâmetro x comprimento 1.500 x 6.000 mm de área. Montei a filial da Cascadura em Salvador”. Aqui abre-se um parêntese, pois ao falar sobre os momentos mais desafiadores da carreira, o executivo apontou novamente o revestimento em cromo duro, entre outros materiais: “Revestir com cromo duro, peças de grande porte, com amperagens de 50.000 Amperes; revestir trocadores de calor de mais de 20 t, internamente com resinas especiais, com cura térmica. Deposição mecânica de latão e cobre em equipamento por mim desenvolvido, que podia depositar mecanicamente latão em 50 minutos sobre 1 t de peças a granel”, detalha.
Cilindro rotogravura cobreado e gravado. Hanns se encantou com TS ao ver seu pai trabalhando com os cilindros
Na década de 1980, Langer atuou como Gerente de Projetos e Manutenção, na Cartográfica Francisco Mazza; como Gerente de Pesquisa e Desenvolvimento, na Galtec; como Pesquisador na Metal Leve (Mahle). Nessa época, ele detalha: “Fiz desenvolvimento de processos eletroquímicos para bronzinas e pistões. Aprimorei ligas ternárias para bronzinas, como anodização dura para topo de pistões de motores pesados. Para isso, fui auxiliado por Microscópico Eletrônico de Varredura. Fui para a Canning, da Inglaterra, para aprimorar processos galvânicos. De 1989 – 1995 fui Gerente da firma AMP (hoje TE Connectivity), minha área era a de galvânica, de projetos e meio ambiente. Fiz viagens de aprimoramento nas filiais dos Estados Unidos e Europa”, conta.
O profissional também passou pela área de vendas e assistência técnica da Atotech (de 1995 até 2005), onde também desenvolveu processos galvânicos e não galvânicos nas matrizes nos Estados Unidos e na Alemanha. “Fiz várias viagens para as Matrizes em Rock Hill, nos Estados Unidos, e em Berlim, Alemanha”, diz. Nessa época, ele destaca uma inovação de sua autoria: “Desenvolvi revestimentos de latão e cobre, por deposição mecânica, para se livrar do cianeto”. Abre-se aqui um novo parêntese, destacando uma das características de trabalho do executivo, que é a sua preocupação com o meio ambiente, atributo que permeou, como prioridade, as suas atividades profissionais.
Nos anos 2000, Langer atuou na Surtec “como Coordenador de Engenharia de Aplicação” e, após, como Gerente de Eng. de Aplicações, na IKG Química e Galtron, em Caxias do Sul (RS), e Campinas (SP). Após, o executivo revela: “Fundei e montei a filial da HSO e da Dicolloy da região de Solingen, Alemanha; em Indaiatuba (SP), que hoje se chama Green Palm Química. Fui Diretor Geral de 2010 a 2012. De 2012 a 2014, trabalhei, não continuamente, na Metal Coat, de Indaiatuba, como Gerente de Pesquisa e Desenvolvimento”. Ali também inovou, desenvolvendo “a partir de matérias-primas intermediárias, aditivos para cobre ácido, níquel brilhante, níquel químico, cromo trivalente decorativos, passivadores de alta camada, etc.”, complementa.
Ao se aposentar não descansou, iniciou sua atividade como Consultor de Galvanoplastia, “desenvolvendo vários processos, como cobre ácido, níquel, cromo trivalente, etc.”, onde atua até hoje. Como ele mesmo diz: “Os objetivos atuais são continuar com o ‘vício’, dando consultoria na área”, reforçando seu encanto pelo setor.
A galvanoplastia levou Hanns a inúmeros lugares físicos e também dentro da própria atividade na qual passou pelas mais diversas áreas, expertise bastante valorizada. Atualmente, mora no interior de São Paulo, em Itu. “Gosto de trabalhar no jardim da minichácara onde moro, onde plantei várias plantas frutíferas e gosto de ficar na natureza, pois na minha infância e juventude fui escoteiro, fazendo proezas, como a de ir a pé de São Paulo a Itanhaém, embrenhando-me na Serra do Mar, sem usar estradas...” Para o seu futuro, ele espera algo que não poderia ser diferente: “Espero poder fazer o que gosto”, finaliza.
Sr. Langer com a esposa e filhos
A família completa
HANNS LANGER FALA SOBRE A INDÚSTRIA
Qual a importância do setor de Tratamento de Superfície para a indústria brasileira? Como o Sr. avalia o setor?
Quase todo objeto que a gente pega nas mãos é feito de algum material e precisa de algum acabamento, se for metálico ou algum plástico como, por exemplo, o ABS, que tem acabamento metálico para servir esteticamente e/ou ser anticorrosão. A Indústria não seria viável sem o setor de tratamento de superfícies.
Atualmente, quais são os grandes desafios do segmento? Quais as principais diferenças para aqueles do passado?
Os grandes desafios de hoje são desenvolver processos que não prejudiquem tanto o meio ambiente e a saúde. Em alguns processos do passado, a gente usava dínamos de corrente contínua, em vez de retificadores, que até cobriam melhor as peças que precisavam ser cromadas. Hoje em dia existem retificadores eletrônicos, com e sem corrente pulsante de onda quadrada, que tem suas vantagens.
O Sr. fez faculdade na Alemanha, um país notório pelo investimento em educação, tecnologia, engenharia e inovação. Quais foram os principais aprendizados aplicados no Brasil? O Sr. acredita que estamos muitos distantes de alcançar a excelência europeia (sobretudo a alemã) em nossas indústrias? Onde podemos melhorar?
Na Alemanha tem muitas restrições a uso indiscriminado de processos químicos, que no Brasil ainda são tolerados, mas que, aos poucos, vão também sendo aplicadas aqui no Brasil devido à globalização. Podemos melhorar usando cromo duro trivalente, deposição em plásticos sem o uso de condicionadores de ácido crômico, e outros produtos químicos que agridam menos o ambiente.
Quais foram as grandes revoluções na indústria vivenciada por você?
Quando comecei a trabalhar na SETECOBEL, nos anos de 1960, não havia abrilhantadores e niveladores nos banhos de cobre ácido. A gente usava um abrilhantamento mecânico, usando uma pedra de ágata, que era aplicada em cima da superfície em um movimento de vai e vem. Alguns anos depois, apareceu o primeiro abrilhantador que se chamava Ubac. Hoje em dia eu mesmo os formulo.
Com tantos anos de experiência, qual o grande aprendizado na indústria?
A vida é um eterno aprender a aprender fazendo! Nem sempre o que fazemos no laboratório se reproduz fielmente na escala de produção industrial.
Como vê o futuro da indústria de Tratamento de Superfície no Brasil? Qual a grande tendência do setor hoje?
Diminuiu muito a quantidade de firmas em funcionamento nas duas últimas décadas e as que continuam funcionando usam tecnologias avançadas. Também aconteceu a fusão de grandes fabricantes de processo no mundo, o que refletiu por aqui; a gente percebe que faltam profissionais experientes em muitas empresas, tanto na produção quanto para controle do processo, e os vendedores experientes já não têm muito tempo para dar assistência técnica – hoje, sair para atender um cliente tem um custo alto. Comparativamente entre o Brasil e Europa, as firmas europeias e americanas têm muito mais pessoal técnico para controlar corretamente a produção, enquanto que, no Brasil, os clientes em geral esperam que essa assistência seja dada pela empresa que vende os processos.
Para finalizarmos, qual a principal dica você pode dar para o executivo industrial no Brasil?
A dica que dou é ter um bom profissional, com bastante prática, para comandar as operações, e usar processos menos prejudiciais ao meio ambiente, para evitar usar equipamentos antipoluentes, de valor elevado.