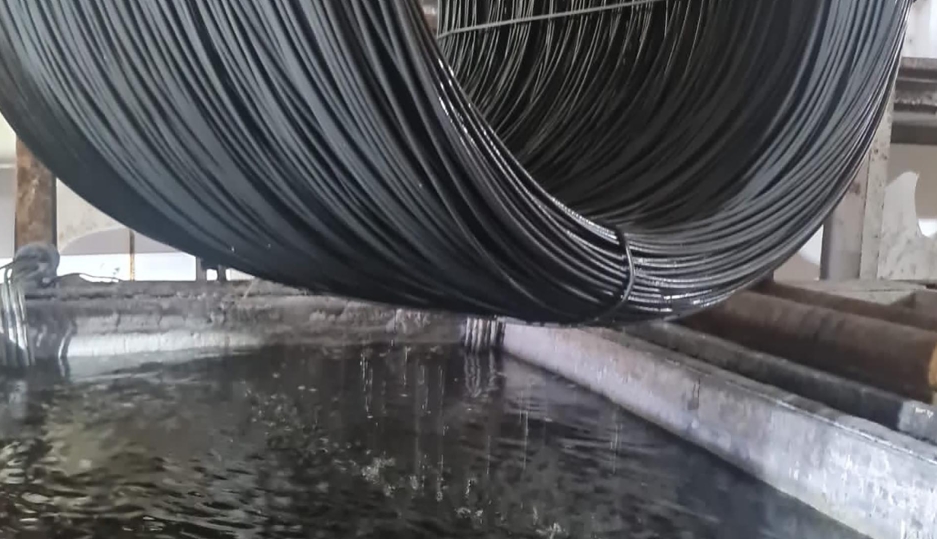
A filosofia de sustentabilidade aplicada nos processos de fosfatização para conformação à frio
Conheça algumas abordagens práticas para que os processos químicos de fosfatização para conformação a frio possam se tornar mais sustentáveis, reduzindo o impacto ambiental e contribuindo para um futuro mais resiliente
1. INTRODUÇÃO
A sustentabilidade refere-se à capacidade de atender as necessidades atuais sem comprometer a capacidade das gerações futuras de suprir suas próprias necessidades. Envolve a busca por um equilíbrio entre as dimensões econômica, ambiental e social, visando a preservação do meio ambiente e o desenvolvimento econômico de forma responsável.
Na dimensão ambiental, a sustentabilidade busca a conservação dos recursos naturais, a redução do consumo de energia, a mitigação das mudanças climáticas, a preservação da biodiversidade e a minimização da geração de resíduos e poluição.
Na dimensão econômica, a sustentabilidade busca a adoção de práticas de negócios responsáveis, a promoção de modelos econômicos circulares e de baixo carbono, o fomento da inovação tecnológica e a criação de empregos verdes e sustentáveis.
O termo ‘sustentabilidade’ tem origem no latim ‘sustentare’, que significa ‘sustentar’ ou ‘manter’. No entanto, o conceito moderno de sustentabilidade, e seu uso mais amplo, surgiu no contexto do desenvolvimento sustentável, popularizado pelo Relatório de Brundtland, em 1987. Oficialmente chamado de ‘Nosso Futuro Comum’, o relatório foi elaborado pela Comissão Mundial sobre Meio Ambiente e Desenvolvimento das Nações Unidas. Ele definiu o desenvolvimento sustentável como “o desenvolvimento que satisfaz as necessidades presentes sem comprometer a capacidade das gerações futuras de satisfazer suas próprias necessidades”. A partir desse relatório, o termo ‘sustentabilidade’ passou a ser amplamente utilizado para descrever a abordagem que busca equilibrar as dimensões Já comentadas.
Para alcançar a sustentabilidade é necessário adotar medidas como a utilização eficiente dos recursos naturais, a promoção da reciclagem e da economia circular, a adoção de energias renováveis, o consumo consciente, a preservação dos ecossistemas e o engajamento da sociedade em ações sustentáveis.
A sustentabilidade é um desafio global que requer a colaboração de governos, empresas, organizações da sociedade civil e indivíduos para a criação de um futuro sustentável e resiliente para todos.
Nos processos de fosfatização para conformação a frio do aço, a filosofia de sustentabilidade quer desempenhar um papel fundamental, pois visa reduzir o impacto ambiental e promover a utilização eficiente e consciente dos recursos naturais. Existem diversas abordagens e princípios que podem ser adotados para tornar esses processos mais sustentáveis. Alguns aspectos importantes a considerar são:
a. Minimização de resíduos: A redução na geração de resíduos é uma meta importante. Isso pode ser alcançado através da otimização dos processos, seleção de materiais menos agressivos e reciclagem de produtos e subprodutos.
b. Uso eficiente de energia: A busca por formas mais eficientes de consumo energético é crucial. Isso pode envolver o uso de tecnologias de baixo consumo energético, aproveitamento de calor residual e a implementação de sistemas de gestão de energia.
c. Conservação da água: A utilização racional da água é fundamental. Estratégias como a recirculação de água, tratamento de efluentes e reutilização podem contribuir para a conservação desse recurso valioso.
d. Avaliação do ciclo de vida: Considerar o ciclo de vida completo dos produtos químicos e processos é importante para avaliar seu impacto ambiental global. Isso envolve desde a extração de matérias-primas até a disposição final dos resíduos.
Este artigo visa mostrar algumas abordagens práticas para que os processos químicos de fosfatização para conformação a frio possam se tornar mais sustentáveis, reduzindo o impacto ambiental, contribuindo para um futuro mais resiliente.
2. RECICLAGEM DE BANHOS DE DESENGRAXE QUÍMICO
A etapa de desengraxe é o processo que consiste em remover, de determinado substrato, sujidades inerentes às etapas anteriores do processo produtivo, na maioria das vezes orgânicas, como óleos, graxas, ceras, resto de pastas de estampagem; e, se for o caso, sujidades inorgânicas, como cavacos ou sais provenientes de processos químicos anteriores. Tem como objetivo a eliminação de todo e qualquer contaminante que não faça parte da superfície da peça para que, em uma segunda etapa, se aplique à camada de fosfato de zinco sem nenhum tipo de problema; mas um inconveniente é constatado: com a utilização constante de banho desengraxante, grande parte dessas sujidades orgânicas são emulsionadas, causando a saturação do banho, implicando na necessidade de sua troca. Esse ponto de saturação dependerá da quantidade de produção e de sujidade a ser removida da superfície metálica, mas é certo que essa saturação ocorrerá, implicando em grandes volumes de efluentes a serem tratados mais utilização de água e produtos químicos para continuação da operação deste estágio de limpeza.
Fotos de banho desengraxante saturado por compostos orgânicos
Há uma enorme variedade de formulações de desengraxantes químicos em utilização no mercado, mas podemos separar a formulação básica de um desengraxante, geralmente, em agentes inorgânicos, responsáveis pela saponificação de óleos e graxas, e orgânicos (surfactantes), responsáveis pela limpeza fina da superfície, englobando a matéria a ser removida da superfície, causando a emulsão e saturação deste banho desengraxante.
Através de pesquisa e desenvolvimento desses processos, hoje, se consegue reciclar esses banhos desengraxantes através da adição de agentes demulgantes aos banhos, esses agentes têm o poder de quebrar todos os complexos e emulsões existentes nos banhos, possibilitando a reutilização da água e da parte inorgânica da solução desengraxante – sendo necessária para a continuação do processo a reposição da parte orgânica.
Fotos de banho desengraxante após a adição de ativos demulgantes
Em resumo: a operação é realizada a qualquer temperatura, adicionando entre 0,1 e 1,0% do volume do banho de agente demulgante, aguarda-se o tempo necessário para a separação de fases, o sobrenadante é removido, a solução é avolumada, são adicionados os surfactantes necessários e o processo pode continuar sua operação de limpeza.
Dependendo da estrutura da instalação, este processo de reciclagem pode ser realizado de forma contínua.
Em um estudo de caso deste processo de reciclagem já em operação, temos o seguinte quadro:
Em questão, temos uma linha na qual seu primeiro estágio é um tanque de desengraxante químico, com volume de 3000 litros, trabalhando de forma contínua (24 horas). Normalmente, a cada 3 meses, devido à saturação da solução desengraxante, era realizada a troca total do banho. Atualmente, nesta mesma linha de processo, é realizada, no mesmo período de três meses, a operação de reciclagem conforme descrita acima, onde foram evidenciados, nesta única etapa do processo de manutenção do sistema de limpeza, os seguintes benefícios:
• 69% menos utilização de produtos químicos;
• 90% menos efluentes gerados para tratamento ou destinação;
• 88% menos utilização de água;
• 77% menos consumo de energia para aquecimento do banho.
3. UTILIZAÇÃO DE INIBIDORES DE DECAPAGEM QUÍMICA DE ALTA PERFORMANCE, VISANDO MELHORA DA VIDA ÚTIL DOS BANHOS DECAPANTES
Nos processos de aplicação de camada de fosfato de zinco visando a conformação a frio, a decapagem ácida é o método mais utilizado para a remoção de óxidos e carepas, provenientes do processo de produção do aço, e/ou tratamentos térmicos anteriores. Essas carepas, apesar de muito aderentes, devem ser removidas de toda a superfície a ser fosfatizada, pois uma de suas caraterísticas é ser altamente microfissurada, inibindo a fosfatização e podendo se desplacar durante o processo de conformação, causando diversos problemas, como falta de lubricidade na região.
Normalmente, a carepa é formada por diferentes camadas de óxidos; sua composição e a espessura variam bastante, dependendo do tempo, temperatura de exposição, composição do aço, composição da atmosfera e agressividade da deformação à quente que foi realizada. Geralmente, a composição da carepa se dá da seguinte forma: primeiramente uma camada externa mais rica em oxigênio, relativamente fina, constituída principalmente de hematita (Fe2O3), seguida de uma camada intermediária, mais grossa, contendo magnetita (Fe3O4.), e, por fim, uma camada mais próxima ao substrato, ainda mais espessa, pobre em oxigênio, basicamente formada de wüstita (composição que se aproxima de FeO).
Os principais agentes utilizados na decapagem química são o ácido clorídrico e o ácido sulfúrico. Por serem ácidos fortes, eles têm alto poder de ataque a oxidações e carepas, devido às suas altas taxas de dissociação.
Fazendo um paralelo entre os componentes da carepa e os principais agentes utilizados para decapagem, a wüstita tem boa solubilidade nos dois agentes, e, quanto maior a concentração do agente, maior a sua solubilidade. A magnetita tem uma solubilidade menor em relação à wüstita; para o ácido clorídrico quanto maior a concentração do agente maior é sua solubilidade, já para o ácido sulfúrico, a concentração em si não tem grandes interferências quanto à dissolução, mas a temperatura da solução sulfúrica, por sua vez, tem grande influência na solubilidade da magnetita. E, por fim, a hematita, é de baixíssima dissolução nos dois agentes e é a grande responsável por formação de borra nos banhos decapantes.
Comparativo entre os dois agentes decapantes:
- Quanto á concentração, para os dois ácidos é bem parecida, 15 a 20% para o HCl e entre 8 e 20% para o H2SO4;
- Superfícies decapadas com ácido clorídrico têm a tendência a ficarem muito mais claras e brilhantes do que superfícies decapadas com ácido sulfúrico;
- O decapante sulfúrico, obrigatoriamente, necessita de aquecimento para uma boa performance, enquanto que o decapante clorídrico, na maioria das aplicações, trabalha em temperatura ambiente;
- Quanto ao consumo desses ácidos, na média para dissolução de 60 g/m² de óxidos, consumimos de 150 a 157g de ácido clorídrico, em sua concentração comercial, de aproximadamente 34 %, e entre 75 e 88g para o ácido sulfúrico;
- Quanto ao teor de ferro contaminante, por características dos agentes, o HCl suporta até 200 g/L enquanto que o decapante sulfúrico, 130 g/L.
O ferro contaminante (apontado no item ‘e’, acima) é uma grande preocupação na etapa de decapagem, pois essa contaminação limita a vida útil do banho decapante, gerando efluentes concentrados de tratamento trabalhoso.
Visando retardar a contaminação por íons de ferro, tendo um ciclo de vida útil do banho decapante saudável, devem ser adicionados agentes inibidores, em doses relativamente baixas; eles têm a principal função de inibir ao máximo o ataque ao substrato sem interferir na remoção de oxidações e carepas. Dependendo de sua formulação, os inibidores também agem na supressão de gases emanados pelo banho decapante. Em materiais a serem decapados com alto teor de carbono, a escolha de um agente inibidor de alta performance é imprescindível para evitar o efeito conhecido como overpickling, ou seja, a formação de fuligem sobre o substrato a ser fosfatizado.
Através de testes específicos, que serão relatados a seguir, pode-se determinar a porcentagem de inibição da solução decapante ao substrato; esta inibição deve sempre tender a 100%, mas nunca atingir esta marca, pois caso aconteça, o banho decapante estará tão inibido que não cumprirá a sua finalidade de remover os óxidos e carepas.
3.1 Teste prático para determinação de eficiência de inibição
- Prova em Branco
Corpo de prova = 2 chapas aço carbono 1010 (35 x 85 mm), devidamente desengraxadas, sem corrosão e secas. Pesar em balança analítica de precisão de 4 casas decimais. Imergir em solução decapante com as seguintes características:
- Prova Inibida
Corpo de prova = 2 chapas aço carbono 1010 (35 x 85 mm), devidamente desengraxadas, sem corrosão e secas. Pesar em balança analítica de precisão de 4 casas decimais. Imergir em solução decapante com as seguintes características:
Decorrido o tempo de imersão, as chapas devem ser lavadas com água e álcool etílico, secas imediatamente e repesadas.
Cálculo para determinação do % de inibição;
Onde:
PiB = Peso inicial em gramas da prova em Branco
PfB = Peso final em gramas da prova em Branco
PiI = Peso inicial em gramas da prova Inibida
PfI = Peso final em gramas da prova Inibida
Considera-se um agente inibidor de alta performance os produtos que tenham o poder de inibição entre 96 e 99%, conforme amostra de referência no gráfico abaixo:
Dessa forma, seguindo o descrito acima, teremos banhos decapantes com um ciclo de vida adequado à filosofia de sustentabilidade, ou seja, um ciclo de vida com o máximo de suas possibilidades, utilizado ao máximo da performance, ótima qualidade de decapagem, não gerando efluentes e resíduos em demasia ou sem necessidade.
4. UTILIZAÇÃO DE BANHOS DE FOSFATO DE ZINCO DE ALTA CAMADA ACELERADOS VIA ÍONS FERROSOS COMO PARTE DA FILOSOFIA DE SUSTENTABILIDADE
Tem-se o histórico da utilização da camada de fosfato de zinco no auxílio à deformação a frio no período pré-Segunda Grande Guerra, sendo empregado em larga escala na Alemanha para a confecção de munição, com seu uso crescendo desde então.
Dentro da conformação mecânica podemos citar vários tipos de processos: trefilação, extrusão e estampagem. Todas essas operações possibilitam dar novas formas ao metal sem a necessidade de pré-aquecimento do material – e em processos em que a temperatura não ultrapasse 500 °C –, tendo, assim, a necessidade de aplicação de camadas de conversão (fosfato de zinco) que, em conjunto com lubrificante específico, vão gerar grande lubricidade durante o trabalho.
O primeiro grande benefício das camadas de fosfato na conformação a frio é proporcionar uma maior retenção de lubrificantes; dependo da rugosidade inicial do substrato e do tipo de lubrificante a ser utilizado, superfícies fosfatizadas podem ter uma retenção 10 vezes superior a superfícies não fosfatizadas, sendo altamente aderentes ao substrato, devido em parte pelo crescimento epitaxial dos grãos de fosfato, evitando o contato metal/metal, ou seja, entre ferramenta e a superfície sendo conformada, aumentando significativamente a vida útil da ferramenta. Essas camadas de fosfato não são ‘arrancadas’ totalmente durante o processo de deformação, como se acreditava anteriormente, na verdade, parte dos cristais de fosfato é transformada em um pó micronizado que, em conjunto como lubrificante, forma uma pasta que se adere sobre a camada remanescente, formando uma superfície hialina.
Por ter uma microdureza próxima ao aço, os cristais de fosfato pouco se desgastam durante o processo de deformação. Com uma deformação de 15%, não se detecta mais a estrutura cristalina inicial e a superfície hialina funciona como uma excelente lubrificante, facilitando ainda mais a deformação subsequente. Após esse estágio inicial, não ocorre mais desgaste da camada, o afinamento da camada de fosfato observado ocorre, simplesmente, devido à extensão da superfície do substrato.
Outro ponto a se destacar é o auxílio significativo na redução do coeficiente de fricção (atrito). De maneira geral, 50% da energia empregada em dada conformação é utilizada na fricção com a utilização da camada de fosfato, e esse número se reduz significativamente. Essas camadas de fosfato de zinco são resistentes às temperaturas de processo, que podem chegar a 500 °C, e, apesar de perderem moléculas de água em sua estrutura, não apresentam grande decomposição para torná-las inaptas ao processo de conformação.
Bobina de fio-máquina fosfatizado com banho de fosfato acelerado via nitrato/ions ferrosos
Tubos de aço fosfatizados com banho de fosfato acelerado via nitrato/nitrito
Há, em utilização no mercado, algumas estruturas de aceleração desta reação de fosfatização. Vejamos.
4.1.Estrutura de aceleração de reação nitrato/nitrito
Este tipo de estrutura de aceleração no banho de fosfato de zinco é a mais utilizada pelo mercado em geral; tem velocidade de reação alta, requerendo tempo de processo entre 5 e 15 minutos de imersão, e trabalha a uma temperatura que varia entre 65 e 85 °C. Tem como resultante camadas de espessura média a alta, com peso de camada que costuma variar entre 8 e 12 g/m².
Nos banhos de estrutura nitrato/nitrito, o principal acelerador é o nitrato, que normalmente vem incorporado à fórmula do fosfatizante (acelerador interno), mas o equilíbrio em relação ao nitrito é indispensável para a boa formação da camada. O nitrito normalmente é adicionado ao banho separadamente (acelerador externo).
O nitrito, além de sua função como acelerador de reação, tem a função de precipitar os íons ferrosos em solução, obtidos através do ataque da acidez livre sobre o substrato, formando assim, a ‘borra de fosfato’. A literatura explica que essa formação de precipitado, nesta estrutura de aceleração, é proporcional à camada de fosfato de zinco depositada, ou seja: se são depositadas 10 g/m² de camada de fosfato de zinco, são formadas 10 g/m² de ‘borra de fosfato’ seca.
Subproduto da reação de fosfatização (Borra de fosfato), da estrutura de aceleração nitrato/nitrito
4.2 Estrutura de aceleração de reação nitrato/íons ferrosos
A concentração de íons ferrosos nesta estrutura, em conjunto com os íons de nitrato, é um parâmetro muito importante, pois é responsável pela correta proporção de formação dos minerais constituintes da camada de fosfato (hopeita e fosfosfilita). Essa proporção é responsável pela aderência e porosidade da camada, sendo alterado este equilíbrio de formação de minerais quando variado o teor ferro.
Com nulas quantidades de ferro, temos uma camada predominantemente formada por hopeita, com pouca aderência; já com leves quantidades, temos a formação proporcional entre hopeita e fosfofilita, camada ideal; e, em concentração muito grande, teremos uma reação tão acelerada que se pode ter inibição de formação de camada.
A camada formada tem um peso entre 8,0 e 20 g/m², com um tempo de aplicação não maior de quinze minutos, e, dependendo de sua formação, é possível trabalhar com temperaturas de aquecimento mais baixas, entre 35 e 70 °C.
Como grande parte desses íons ferrosos, obtidos através do ataque ao metal-base, permanecem em solução para acelerar a reação de fosfatização, a formação de ‘borra de fosfato’ será consideravelmente menor em relação a um fosfato de zinco acelerado pela estrutura nitrato/nitrito. A formação desse resíduo se dará por oxidação dos íons ferrosos em troca com a superfície do banho e em uma eventual necessidade de baixar o teor de ferro deste banho de fosfato de zinco.
Voltando à questão da implantação da filosofia de sustentabilidade nos processos de fosfatização para conformação a frio do aço, em muitos dos processos de conformação, podemos utilizar fosfatos de zinco com aceleração via íons ferrosos em vez dos banhos de aceleração nitrato/nitrito, mantendo a qualidade de conformação do material pela camada obtida, mas com menor formação de borra de fosfato, como resíduos para destinação.
Lembrando que a ‘borra de fosfato’ normalmente é classificada como ‘resíduos classe II’ (NBR 10004), devendo ser destinada apropriadamente – logo, quanto menor a formação desse resíduo, mais sustentáveis serão os processos de fosfatização com a finalidade de conformação a frio. Existem formulações que trabalham a baixas temperaturas, obtendo camadas de fosfato de zinco de qualidade, contribuindo, assim, com a premissa do uso consciente de energia.
5. FILOSOFIA SUSTENTS
A Filosofia SustenTS é um método de trabalho para processos de tratamento de superfície desenvolvido seguindo as premissas de sustentabilidade que são objetivadas mundialmente, onde, através da capabilidade e eficiência de produção, os processos de fosfatização da conformação a frio do aço se tornarão cada vez mais sustentáveis, gerando menos resíduos e efluentes, mantendo a qualidade total do processo. Saiba mais em SustenTS.com
6. CONSIDERAÇÕES FINAIS
A busca da indústria pela sustentabilidade é uma tendência cada vez mais presente e necessária. As empresas estão percebendo a importância de se adotar práticas sustentáveis não apenas como uma responsabilidade social, mas também como uma estratégia de negócio inteligente.
Existem várias razões pelas quais a indústria está buscando a sustentabilidade. Uma delas é a crescente conscientização sobre os impactos ambientais das atividades industriais. A poluição, o esgotamento dos recursos naturais e as mudanças climáticas têm efeitos significativos no planeta e na sociedade como um todo. As empresas estão percebendo que precisam tomar medidas para reduzir seu impacto ambiental e contribuir para um futuro mais sustentável. Ademais, a busca pela sustentabilidade também traz benefícios econômicos para as indústrias.
A eficiência energética, a redução de desperdícios, o uso de materiais recicláveis e a adoção de processos mais limpos podem resultar em economia de custos a longo prazo. Além disso, muitos consumidores estão valorizando cada vez mais empresas que se comprometem com a sustentabilidade, o que pode gerar vantagem competitiva e fortalecer a imagem da marca.
As regulamentações governamentais também estão se tornando mais rigorosas em relação à proteção ambiental, o que obriga as indústrias a se adaptarem e implementarem práticas mais sustentáveis. Ao antecipar essas regulamentações e adotar medidas proativas, as empresas podem evitar problemas legais e financeiros futuros.
Em resumo, a busca da indústria pela sustentabilidade é impulsionada por uma combinação de responsabilidade ambiental, benefícios econômicos e conformidade regulatória. As empresas estão percebendo que é possível crescer e ter sucesso de maneira sustentável, adotando práticas e tecnologias que reduzem o impacto ambiental, promovem a eficiência e contribuem para um futuro mais equilibrado.