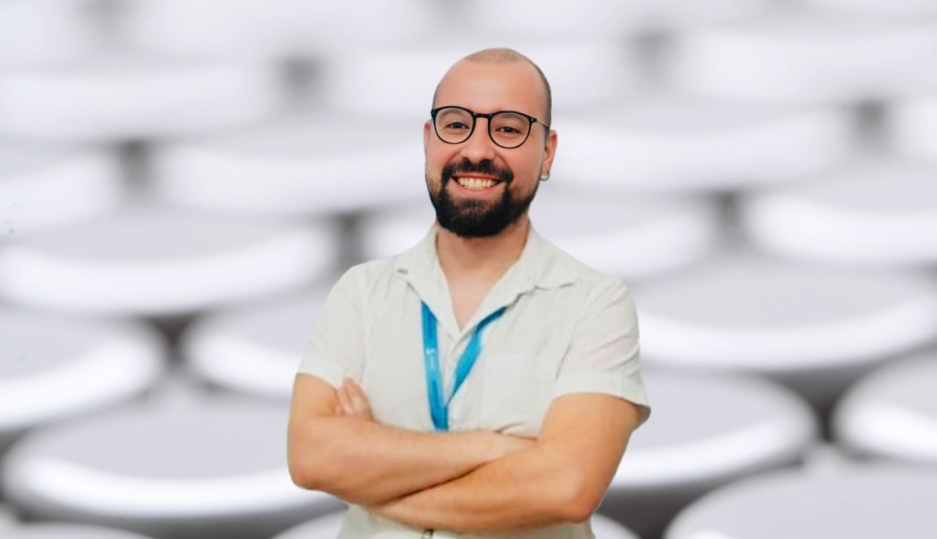
Lucas Teruel Luz, Technical Service Specialist da Syensqo
O aço galvanizado por imersão a quente consiste em uma camada de zinco que protege o aço e pode prevenir a corrosão em muitas circunstâncias. A galvanização oferece vários benefícios:
- Possibilidade de prolongar a vida útil das peças controlando a espessura do depósito de zinco;
- Proteção total das peças (mesmo em locais inacessíveis graças à técnica de imersão em banho líquido);
- Efeito barreira contra a corrosão, que reduz a velocidade de corrosão (tela física entre aço e agentes agressivos);
- A camada de Zn atua como ânodo de sacrifício em caso de danos, revelando o substrato de aço (acoplamento galvânico que permite oxidar, preferencialmente, o zinco em vez do aço porque o zinco é mais anódico do que o ferro).
O revestimento que se desenvolve durante o processo de galvanização é ligado metalurgicamente ao aço, tornando-se virtualmente parte do próprio aço. Durante a reação na caldeira, o zinco interage com o ferro do aço para formar uma série de camadas de liga de zinco-ferro. A fotomicrografia é um corte transversal do revestimento de aço galvanizado, mostrando uma microestrutura típica composta por três camadas de liga e uma camada de zinco metálico puro.
Figura 1. Típicas camadas intermetálicas presentes em um aço galvanizado por imersão a quente. As camadas intermetálicas típicas são:
- A fina camada Gamma, composta por uma liga de 75% de zinco e 25% de ferro;
- A camada Delta, composta por uma liga de 90% de zinco e 10% de ferro;
- A camada Zeta, composta por uma liga de 94% de zinco e 6% de ferro;
- A camada externa Eta, que é composta de zinco puro.
O mercado atual exige uma altíssima qualidade do aço, especialmente quando se trata de durabilidade e resistência à corrosão, que adquire ainda mais prevenção com a galvanização. Fatores como o aumento da demanda nos setores da construção civil, decoração, eletrodomésticos; aumento de volume de aço galvanizado a quente, ou HDG, como é comumente conhecido, de alta qualidade, especialmente para aplicação em construção e exteriores, devido ao aumento da qualidade de vida da população, são alguns dos fatores que levaram os fornecedores de aço a buscarem tecnologias de tratamentos de conversão química do substrato para atenderem a essas demandas.
As conversões químicas são úteis por vários motivos, entre eles:
- Estética: exemplo de cromatização em galvanização à quente/eletrogalvanização HDG/EG (ex: fixadores/parafusos/etc.);
- Resistência à corrosão: para melhorar as propriedades preventivas de deterioração dos substratos;
- Adesão da tinta: para reforçar as interações (ligações) entre a tinta orgânica e o substrato.
As tecnologias tradicionais para tratamento de superfícies metálicas são as de fosfatização, cromatização e oxalação, baseando-se nos seus principais constituintes: fosfatos, cromatos e oxalatos, respectivamente; além das tradicionais, outras vêm sendo desenvolvidas e aprimoradas, como por exemplo a chamada ‘tecnologia nano’. A tecnologia de cromatização se popularizou como solução para endereçar a necessidade de melhora na qualidade do HDG, devido à sua alta performance técnica e robustez em seu processo. Contudo, podemos destacar os seguintes pontos negativos da utilização de produtos à base de cromo para o tratamento de superfícies metálicas, incluindo o HDG:
- O cromo hexavalente (CrVI) pode causar câncer, é considerado tóxico com efeitos duradouros e pode causar reações alérgicas na pele;
- O CrVI está sujeito às restrições da ECHA (Agência Europeia das Substâncias Químicas) e se enquadra nos Anexos XVII e XIV, na Europa, limitando o seu registro no REACH;
- O uso de CrVI é proibido no setor automotivo na Europa: Diretiva 2000/53/EC - a ‘Diretiva ELV’;
- O controle de fósforo no descarte de águas residuais está se tornando mais rigoroso na China, Coreia, EUA, e muitos outros países;
- O custo do tratamento de resíduos químicos aumenta constantemente de maneira global.
Entre as tecnologias alternativas para substituição de produtos à base de Cromo, o processo de fosfatização se popularizou, com uma performance técnica muito boa em sua proteção à corrosão e adesão de tintas. Apesar da excelente performance, alta adesão do mercado (especialmente o automotivo) e melhora no quesito segurança ocupacional, os processos de fosfatização acabaram também apresentando algumas desvantagens importantes. Um exemplo é a alta geração de efluentes, que gera um custo elevado para o seu tratamento e, em casos de fosfatação contínua e em grande escala, a manutenção dos parâmetros do banho e funcionamento em um nível ideal é um processo fundamental e complicado.
Além disso, a partir do momento em que a sustentabilidade passou a ocupar um espaço importante e de destaque nas metas de crescimento das grandes empresas, fez-se necessário o desenvolvimento de novas tecnologias. As principais motivações que levaram a essa busca foram a redução do consumo de energia (devido à temperatura em que os banhos de fosfatização operam), diminuição na geração de lodo e efluente para baratear o custo do processo, e facilitação do controle do processo em si, por conta de sua sensibilidade. Dentre essas novas tecnologias, a utilização da ‘tecnologia nano’, como ficou popularmente conhecida no mercado, tem ganhado cada vez mais espaço. A tecnologia utiliza hexafluoretos de titânio e/ou zircônio para criar uma camada de conversão ao reagir com as superfícies metálicas; e tem como principais vantagens:
- A sua relativa simplicidade de operação e baixa geração de resíduos e efluentes, especialmente se comparada às tecnologias mencionadas anteriormente;
- Operação do processo à temperatura ambiente, reduzindo o consumo de energia.
Apesar de resolver as questões ambientais e de segurança ocupacional, a performance técnica da tecnologia, especialmente a adesão de tintas, não era superior aos processos tradicionais utilizando sais de Cr e fosfatização. Assim, a evolução tecnológica continuou a partir da combinação de aditivos químicos combinados com os hexafluoretos de titânio e/ou zircônio. Na Figura 2, pode-se verificar uma avaliação de performance das diferentes tecnologias mencionadas.
Figura 2. Esquema das diferentes tecnologias para conversão química de superfícies metálicas. Apresenta um comparativo entre as tecnologias de conversão química, destacando as diferenças em eficácia, impacto ambiental, e complexidade técnica.
A otimização da adesão de tintas em superfícies pode ser obtida através de vários mecanismos; entre eles, podemos destacar:
- Desengraxe da superfície, a fim de se remover óleos, partículas e sujidades provenientes de etapas anteriores;
- Criação/aumento de rugosidade da superfície através de processos químicos ou físicos;
- Utilização de aditivos químicos que funcionam como ‘ponte’ entre a superfície metálica e a tinta.
A utilização de determinados aditivos pode melhorar muito a adesão da tinta na superfície metálica e isso é possível devido às fortes interações entre os grupos químicos presentes nesses aditivos. Os polímeros bifuncionais desempenham muito bem esse papel através da escolha correta dos grupos que compõem a sua estrutura. Esses grupos podem formar ligações químicas ou interagir fortemente com a tinta e o substrato com conversor de camada, conforme a figura abaixo.
Figura 3. Esquema dos diferentes mecanismos para melhorar a adesão de tintas na superfície metálica. Ilustra as técnicas utilizadas para aumentar a adesão entre a tinta e a superfície metálica, como o desengraxe, a criação de rugosidade, e a aplicação de aditivos químicos.
Estudos realizados utilizando espectroscopia de emissão ótica por descarga luminescente (GD-OES) conseguiram demonstrar que esses polímeros bifuncionais, combinados com hexafluoretos de titânio e/ou zircônio, estão presentes na superfície do HDG. O polímero bifuncional está presente na interface entre a tinta e a camada de conversão, sendo o responsável pela ponte entre ambas. Isso é importante, uma vez que a melhora na performance de resistência à corrosão e adesão de tinta é proveniente dessas fortes interações entre o polímero, a tinta e a camada de conversão (Figura 5).
Figura 4. Esquema das interações entre polímeros bifuncionais, superfícies com conversores de camada e tinta. Mostra como os polímeros bifuncionais agem como pontes entre a superfície metálica e a tinta, melhorando a adesão e resistência à corrosão.
A fim de se demonstrar a eficiência desses polímeros bifuncionais na melhora da performance de resistência à corrosão e adesão de tinta no tratamento de perfis de HDG utilizados na construção civil foram simulados, em escala de laboratório, processos de tratamento desses substratos (Figura 6).
Figura 5. Esquema representativo de um espectro de GD-OES após o tratamento de HDG com um conversor de camada à base de hexafluoretos de titânio e/ou zircônio combinados com um polímero bifuncional. Demonstração da presença de polímeros bifuncionais na interface entre a tinta e a camada de conversão.
Os polímeros bifuncionais podem ser utilizados em 3 etapas do processo:
- Combinado com o conversor de camada (base Ti/Zr);
- Na etapa de selagem;
- No enxágue final.
Essa robustez, na utilização do polímero bifuncional, confere uma vantagem ao formulador, uma vez que sua utilização pode ser adaptada ao tipo de linha em que ele será utilizado.
Para a avaliação da performance foram utilizados os seguintes testes:
- Atmosfera de condensação com umidade constante (ISO 6270-2) - Envelhecimento a 40 °C, >98% umidade relativa, durante 10 dias;
- Teste de Cupping (ISO 1520) e teste de impacto (ISO 6272);
- Teste de névoa salina neutra (NSS) (ISO 9227), com tinta em pó PE - Exposição a 35 °C entre 500 e 1000 horas;
- Avaliação da delaminação ao longo do corte (ISO 4628-2/-8).
Para sumarização dos resultados foram elaborados gráficos do tipo aranha com notas de 0 (pior resultado) a 10 (melhor resultado). As avaliações de cada um dos testes foram adaptadas para se enquadrarem na classificação de 0 a 10, conforme figura abaixo:
Figura 6. Esquema dos diferentes processos envolvidos no tratamento de HDG para pintura. Descreve as etapas e técnicas envolvidas no tratamento do aço galvanizado para preparação antes da pintura.
O primeiro estudo de caso foi realizado com adição de 2 concentrações do polímero bifuncional, Addibond 106, desenvolvido pela Solvay, em combinação com Ti/Zr em formulações de diferentes pH. A aplicação da camada de conversão foi por imersão e o processo está descrito na Figura 7.
Figura 7. Processo utilizado para o estudo de caso #1 e #2. Detalha os passos específicos e as condições usadas nos estudos de caso, incluindo a aplicação da camada de conversão e as variações de pH testadas.
Seguem os resultados obtidos nos testes de impacto e Cupping:
Figura 8. Resultados obtidos nos testes de impacto e Cupping nas diferentes condições testadas. Apresenta os resultados dos testes realizados sob diferentes condições, destacando o impacto do pH na performance dos revestimentos.
Para ambos os testes, o pH teve um efeito muito significativo na performance, aumentando a performance com o decréscimo do pH.
Para o tratamento apenas com Ti/Zr, apesar de ser melhor que os resultados obtidos apenas com o desengraxe, todos os outros tratamentos obtiveram resultados bastante superiores nos testes de Cupping. Nos testes de impacto, ao se ajustar o pH para 3,0, foi possível obter resultados superiores ao tratamento apenas com Ti/Zr.
Na Figura 9, seguem os resultados obtidos nos testes de NSS após 500h, juntamente com a avaliação de Cupping e impacto mencionadas anteriormente.
Figura 9. Gráfico do tipo aranha comparando a performance dos diferentes tipos de tratamentos realizados. Mostra uma comparação visual da eficácia de diferentes tratamentos, incluindo resistência à corrosão e adesão da tinta, em um formato de gráfico de aranha.
Pelos gráficos a seguir, nota-se que é possível aumentar a resistência à corrosão (pelos eixos de tamanho e densidade dos blísteres formados), além de uma performance superior nos testes de adesão úmida (Cupping e impacto) ao combinar Addibond 106 com Ti/Zr.
O segundo estudo de caso foi realizado seguindo o mesmo processo, mas, desta vez, em vez da aplicação da camada de conversão por imersão, foi aplicada por spray em escala piloto. Seguem os resultados obtidos nos testes de adesão úmida na Figura 10.
Figura 10. Resultados obtidos nos testes de impacto e Cupping nas diferentes condições testadas. Detalha os resultados dos testes de impacto e Cupping para o segundo estudo de caso, mostrando a eficácia do tratamento quando aplicado por spray.
Todas as condições testadas apresentaram performance superior ao tratamento apenas com o desengraxe e, para os testes de Cupping, a adição do Addibond 106, em diferentes concentrações, resultou em uma melhora no resultado do teste.
Figura 11. Gráfico do tipo aranha comparando a performance dos diferentes tipos de tratamentos realizados. Analisa a performance de diferentes tratamentos com base em vários critérios, ilustrados em um gráfico de aranha para facilitar a comparação visual.
Pelos gráficos da Figura 11 é possível verificar que a adição de Addibond 106 reduziu a densidade dos blísteres formados, sendo o tratamento com 2500 ppm o mais eficiente.
No terceiro, e último estudo de caso, foi realizada avaliação com a adição do Addibond 106 na etapa de passivação, após o tratamento com Ti/Zr; segue, abaixo, o esquema do processo utilizado:
Figura 12. Processo utilizado para o estudo de caso #3. Explica o procedimento específico adotado para o terceiro estudo de caso, incluindo as fases de tratamento e as condições experimentais.
Seguem os resultados obtidos nos testes de impacto e Cupping:
Figura 13. Resultados obtidos nos testes de impacto e Cupping nas diferentes condições testadas. Apresenta os resultados dos testes de impacto e Cupping para o terceiro estudo de caso, destacando a eficácia da adição de Addibond 106.
Para ambos os testes, a adição de 2500 ppm de Addibond 106 apresentou melhora significativa nos resultados, conforme podemos observar na Figura 13. Segue o gráfico aranha com os resultados de NSS (Névoa Salina Neutra), na Figura 14.
Figura 14. Gráfico do tipo aranha comparando a performance dos diferentes tipos de tratamentos realizados. Compara a eficácia de diferentes tratamentos com base em múltiplos critérios de desempenho, evidenciando a influência do Addibond 106.
Pelos resultados obtidos no gráfico aranha da Figura 14, nota-se o grande impacto na performance da adesão úmida ao se adicionar Addibond 106 e isso sem comprometer a performance de corrosão por NSS (Névoa Salina Neutra).
A partir dos resultados dos três estudos de caso foi possível comprovar a eficiência da utilização de polímeros bifuncionais para aumentar a performance de adesão de tintas e prevenção à corrosão no tratamento de HDG. Segue um resumo dos resultados obtidos nos três estudos de caso:
Figura 15. Resumo dos resultados obtidos nos três estudos de caso utilizando Addibond 106 como aditivo no tratamento de HDG. Apresenta um resumo consolidado dos efeitos positivos do Addibond 106 em diferentes aplicações e condições.
Os maiores resultados foram obtidos ao se utilizar o Addibond 106 juntamente com o conversor de camada e aplicado por spray, porém, os resultados podem ser otimizados pelos formuladores para se obter soluções que atendam às diferentes especificações.
Em resumo, a priorização da sustentabilidade e novas regulamentações trazem desafios para formuladores de tratamento de metais. Polímeros bifuncionais da linha Addibond são aditivos excepcionais que podem ajudar os formuladores a atender às crescentes exigências do mercado sem comprometer o meio ambiente e a segurança dos operadores. Os produtos da linha Addibond são versáteis e podem se adaptar aos mais diferentes processos utilizados no tratamento dos mais diversos substratos metálicos.
Bibliografia
- S.M.A. Shibli, B.N. Meena, R. Remya, Surface & Coatings Technology 262 (2015) 210–215.
- AGA (American Galvanizers Association) - The HDG Coating
- T.S.N. Sankara Narayanan, Rev.Adv.Mater.Sci. 9 (2005) 130-177
- I. Milošev and G. S. Frankel 2018 J. Electrochem. Soc. 165 C127