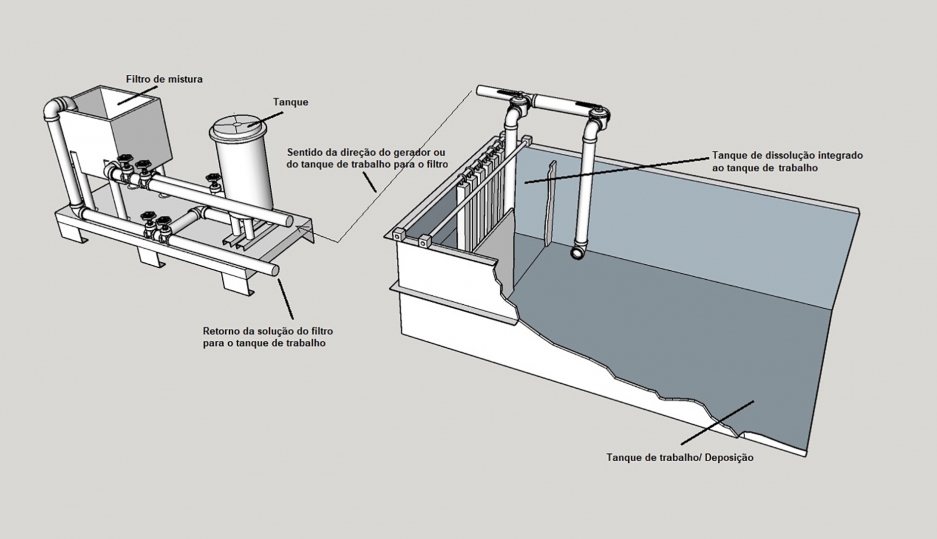
Todos os passos para você instalar o tanque que vem sendo cada vez mais utilizado e melhorar a sua produção já!
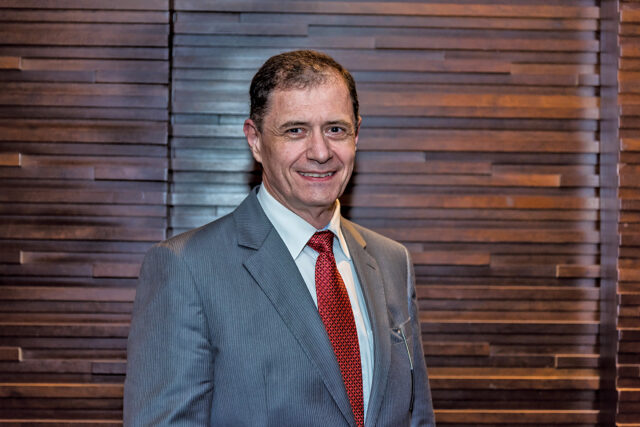
Tradução: Douglas de Brito Bandeira, da Metal Coat Produtos Químicos
Robert Ludwig e Rick Holland
Columbia Chemical Corp., Cleveland – EUA.
Zincagem é um dos processos de maior volume na indústria de eletrodeposição, e o uso de zinco alcalino isento de cianetos é o que mais cresceu dentro desse segmento. Essa ocorrência está sendo influenciada pelo aumento das preocupações ambientais e de segurança associadas aos eletrólitos com cianetos.
Os atuais eletrólitos alcalinos isentos de cianetos se comparam aos cianídricos em relação a brilho, poder de penetração e ductilidade, sem os riscos relacionados ao cianeto. Esses banhos ainda oferecem custos operacionais mais baixos que os eletrólitos ácidos à base de cloreto de zinco, além de oferecer depósitos mais uniformes com relação à camada nas diferentes densidades de corrente.
Com o crescimento do uso desse tipo de tecnologia ocorre uma mudança no pensamento tradicional sobre tipo de ânodos e o reabastecimento de zinco metálico no banho de tratamento. Os eletrólitos de zinco alcalino isento de cianetos requerem um controle mais rigoroso das concentrações de metal dissolvido do que nas soluções cianídricas.
O conceito de uso de ânodos de aço inerte e um tanque ‘gerador de zinco’ separado, no lugar dos ânodos tradicionais nesses processos, já existe há muitos anos, no entanto, até recentemente, a disponibilidade de projetos práticos e experiência de campo era menos do que adequada. Este artigo aborda as vantagens de uso de um tanque gerador de zinco e fornece informações práticas para projetos.
Reforço do zinco
O zinco pode ser reposto nas soluções alcalinas isentas de cianeto da mesma forma que usualmente se faz nas soluções cianídricas – ou com o uso de tanques de dissolução em separado, contendo uma solução de hidróxido de sódio. Essa solução rica em zinco é, então, circulada para o tanque de deposição. Diferentemente dos banhos de zinco cianídricos, os sais não dissolvidos não devem ser adicionados diretamente às soluções de zinco alcalino isentos de cianetos.
As formas mais populares de ânodos de zinco utilizadas são as de bolas em cestos de aço ou placas/lingotes – que podem estar em cestos ou pendurados em ganchos de aço nos barramentos anódicos. No entanto, os operadores de processo chegaram à conclusão de que o uso de ânodos de zinco dentro dos tanques de eletrodeposição, como forma única de reposição de metal na solução, pode ser inadequado, e até problemático. A ausência de cianeto deixa mais limitado o poder de dissolução da solução, então, controles mais rígidos são necessários para manter estável a concentração de zinco, especialmente, conforme a produtividade aumenta. Normalmente, para quem opera o processo, é praticamente impossível monitorar e controlar todos os fatores que influenciam a concentração de zinco em uma solução alcalina sem cianeto diariamente: área de ânodo de zinco, arraste da solução, corrente elétrica, temperatura da solução, quantidade de hidróxido, área catódica e volume de serviço a ser beneficiado.
Além disso, quando se torna necessário ajustar a quantidade de zinco na solução, é obrigatório adicionar ou remover fisicamente os ânodos e também ajustar a quantidade de hidróxidos na solução. Também mais testes de monitoramento e controle se fazem necessários para determinar outras correções adicionais.
Tanques de dissolução de zinco
A reposição de metal com um pequeno tanque de dissolução contendo ânodos de zinco com hidróxido de sódio, e utilizando placas de aço como ânodos no tanque de deposição, confere ao operador muito mais controle do que depender simplesmente da dissolução do zinco no tanque de trabalho.
Vantagens adicionais dessa técnica incluem o seguinte:
- O tempo associado aos testes da solução são reduzidos;
- Existe um controle separado da solução de trabalho e da solução de reforço;
- Está disponível reforço de zinco com ação imediata para o tanque, assim como reserva para futuras reposições;
- Uma forma simples e relativamente rápida de aumentar ou diminuir a concentração de zinco está disponível para diferentes tipos de peças ou diferentes solicitações na operação;
- O uso de lingotes de zinco em vez de metal em bolas é possível;
- A possibilidade de polarização de ânodos, que pode contribuir com formação de aspereza nas peças, é evitada.
A instalação de um tanque de dissolução no processo de zinco alcalino isento de cianetos não irá resolver todas as preocupações do operador. A preocupação com limpeza apropriada anterior ao tratamento, e com o monitoramento e controle dos efluentes continuará. Mas, mesmo assim, irá simplificar a operação e estabilizar o banho, produzindo com brilho e uniformidade no dia a dia.
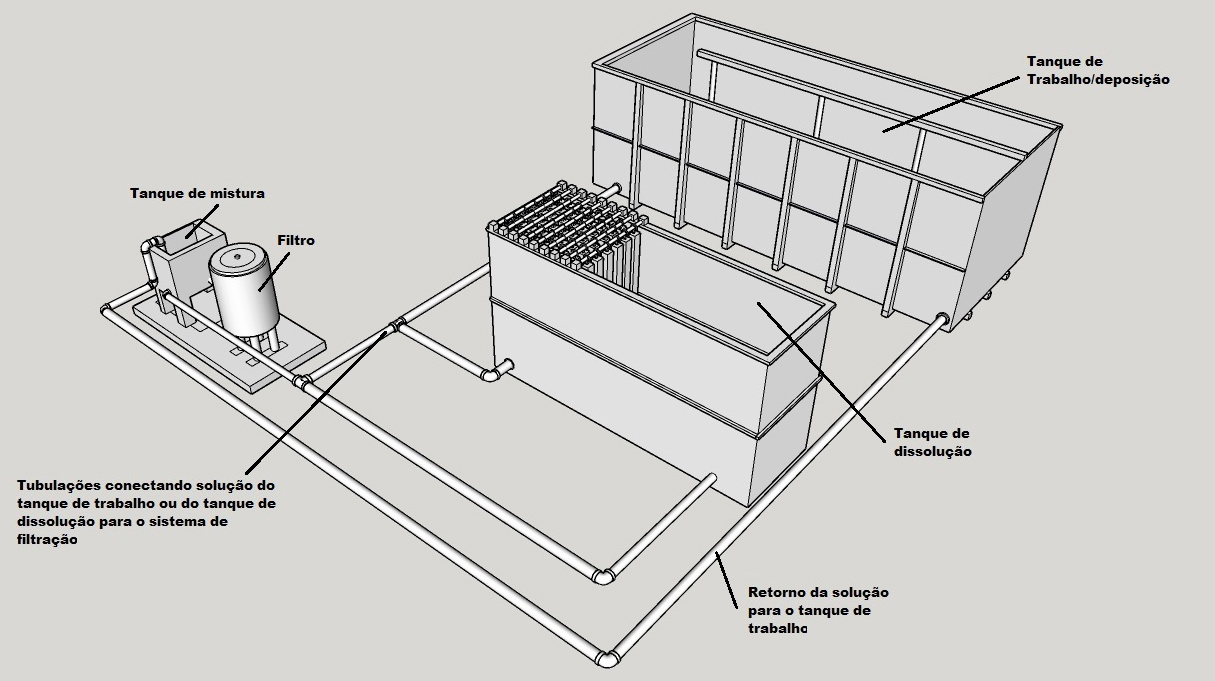
de cestos de aço carbono cheios de zinco em bolas.
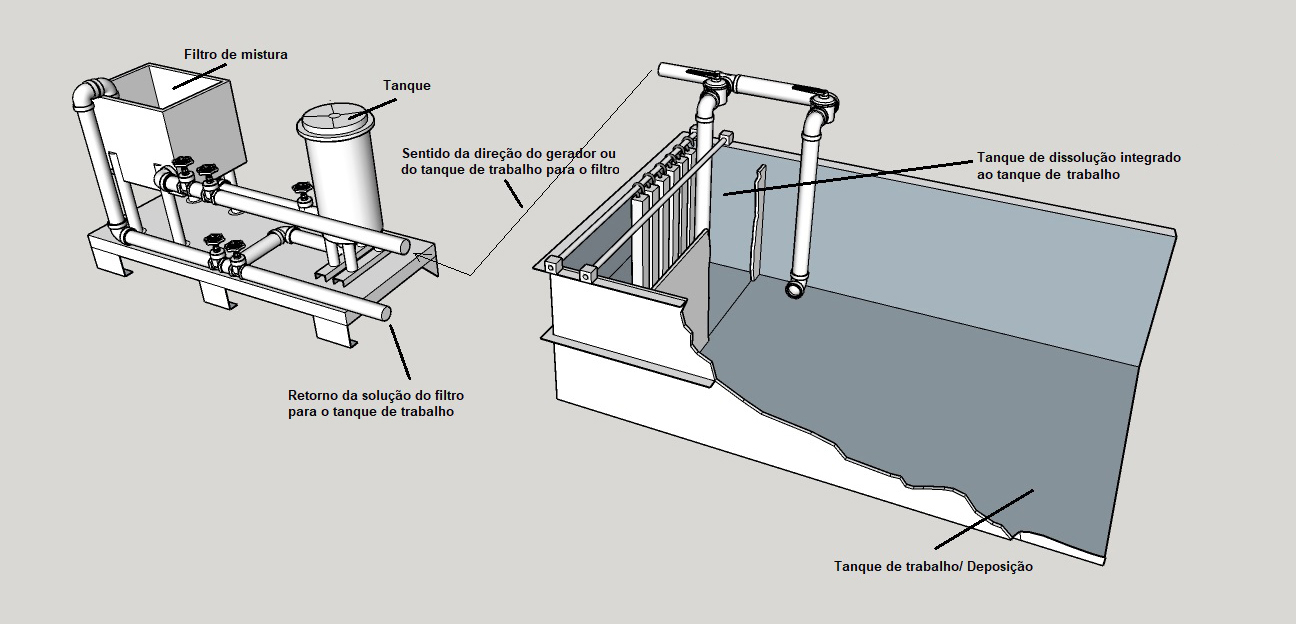
Tanque de dissolução é necessário??
Certos fatores da operação de zincagem determinarão o quanto será importante o uso de um tanque de dissolução para a linha. O gerador de zinco geralmente se comprova como extremamente benéfico, tanto para linhas rotativas quanto de gancheiras. Considere as seguintes questões antes de montar um tanque de dissolução de zinco:
- A linha de zincagem será de alto volume?
- As peças processadas podem ser consideradas como ’responsáveis por grande arraste’?
- As peças a serem tratadas utilizaram uma corrente relativamente alta?
- A linha de zincagem trabalhará todos os dias?
- Existe espaço adequado para o tanque de dissolução?
Se a resposta for ‘sim’ para qualquer uma dessas perguntas, então, o uso do tanque de dissolução parece ser indicado.
O zinco é depositado e arrastado como efluente em diferentes medidas, dependendo das peças processadas e do ciclo de trabalho da linha. Operadores do processo, utilizando zinco em bolas ou placas/lingotes como ânodos, vão concluir que, continuamente trabalhando com altos volumes ou alta densidade de corrente, será quase impossível manter estável a concentração de zinco no banho. Após há apenas algumas horas de trabalho será necessário aumentar a área de ânodos de zinco e/ou a concentração de soda dentro do banho. Depois de alguns períodos ociosos, provavelmente, será necessário retirar ânodos do banho, pois, mesmo não trabalhando, o zinco continuará se dissolvendo e aumentando sua concentração na solução. Eventualmente, tempos de parada de produção ou de baixa produtividade podem ocorrer, aguardando que o banho retorne em sua faixa ideal de trabalho.
Uniformidade da camada depositada também é um problema. Uma linha típica de zinco alcalino isento de cianeto que tem ânodos de zinco na solução de trabalho pode iniciar a semana com concentrações de zinco entre 11 e 12 g/l e, após 8 horas de trabalho, por exemplo, a cada dia da semana, cairá a concentração na solução para 6 a 7 g/l. Frequentemente, os operadores desse sistema são obrigados a contar com a parada de produção durante o fim de semana (e, às vezes, durante a semana de forma não programada) para repor o zinco na solução de trabalho.
De forma contrária, linhas com alta produção e alto arraste de solução são capazes de trabalhar continuamente sem paradas eventuais de ajuste – isso se estão fazendo uso de tanques apropriados de dissolução.
Galvânicas que utilizam os tanques de dissolução também contam com eletrólitos de trabalho muito mais estáveis, durante toda a semana, com relação à concentração de zinco, resultando em muito mais qualidade de trabalho.
Reduzindo a variação na concentração de zinco metal, o sistema de aditivos do processo fica mais eficiente e mais constante quanto ao consumo e às características de depósito, e também torna possível alterar rapidamente a concentração de zinco na solução de forma a atender diferentes necessidades em diferentes tipos de peça a beneficiar.
Projeto do tanque de dissolução de zinco
Projetar um pequeno tanque de dissolução de zinco contendo uma solução altamente concentrada de hidróxido de sódio (115 a 165 g/l), e uma ampla quantidade de zinco, permitirá ao zincador circular a solução concentrada de zinco para o banho e manter concentrações estáveis do minério com facilidade.
A primeira diretiva é a de que o zinco no tanque de dissolução esteja em contato constante com as cestas e placas de aço carbono. Isso formará uma célula galvânica que permite que o zinco se dissolva rapidamente, e com uma taxa uniforme de dissolução. Se o zinco metálico não estiver em contato com o aço carbono, a dissolução será lenta prejudicando o fornecimento de zinco dissolvido no processo.
Em seguida, a agitação a ar e bomba de circulação interna ou externa para transferir a solução de zincato continuamente do tanque de dissolução. A não movimentação adequada da solução fará com que os lingotes, placas ou bolas de zinco formem uma crosta de óxidos/hidróxidos de zinco que poderão impedir a sua dissolução. Se ocorrer a formação dessa crosta, ela deve ser removida ou o zinco não se dissolverá da forma prevista.
Um tanque de dissolução bem projetado possibilita acesso fácil para reabastecimento do zinco metálico e reforço do hidróxido de sódio. Normalmente, as linhas de zincagem com um tanque de dissolução não necessitam de reposições de hidróxido de sódio no taque de deposição. Tanto o zinco como a soda cáustica são fornecidos pelo tanque de dissolução. Manter linhas com suprimento adequado de zinco resulta em diferentes formas de operação do sistema. Linhas de alto volume de produção necessitam de tanques de dissolução de maior volume, linhas com baixo volume de produção, ou ociosidade, já não necessitam de tanto volume. O volume médio de um tanque de dissolução varia de 15 a 20% do volume total do tanque de deposição. Em alguns casos de produção muito alta, os volumes dos tanques de dissolução chegam a 33% do volume do tanque de zincagem.
Para determinar o tamanho do tanque de dissolução ideal, o fornecedor deve levar em consideração o volume de produção, o tempo de banho e as limitações de espaço da linha. Para instalar um tanque de dissolução que tenha de 15 a 20% do volume do tanque de trabalho, o zincador deve prever espaço para o tanque, filtros, bombas, sistema de exaustão para vapores e encanamento para circulação da solução entre o tanque de trabalho e o de dissolução.
Normalmente, o tanque de dissolução fica localizado próximo ao tanque de deposição conectado com entrada e retorno de solução através de encanamento e bombas adequadas. Preferencialmente, a posição do encanamento deve possibilitar que a solução retorne do tanque de trabalho por gravidade para evitar custos extras, de bombas por exemplo (consulte as figuras 1 e 2). Para remover partículas de zinco não dissolvidas que possam causar aspereza no processo, utiliza-se filtro antes do tanque de deposição.
A construção do tanque de dissolução de zinco
Os tanques de dissolução são construídos em aço carbono. Cestos e ou divisórias, também de aço, são instalados nos tanques, fornecendo área de retenção para as bolas ou placas de zinco. Os cestos e placas de aço devem ser removíveis para fornecer espaço para a manutenção e alcance para alguma operação dentro do tanque.
As cestas e chapas de aço carbono devem ser aquecidas ao fogo antes da instalação. O filme de óxido azulado, resultante da exposição ao fogo, atua como um catalizador na dissolução do zinco. As placas de contato podem ser de aço expandido (muito utilizado em passarelas nas linhas de revestimento). O encanamento que conecta o tanque de zincagem ao tanque de geração de zinco deve permitir que a solução se desloque livremente de um tanque para o outro. A posição de instalação adequada das bombas e filtros garantirá o fluxo e circulação adequados da solução de zincato, assim como o controle da concentração de zinco no tanque de deposição.
Existem vários métodos de agitação da solução. Ar comprimido, através de tubos perfurados no fundo do tanque de dissolução, fornece excelente movimentação da solução e permite uma boa dissolução do zinco. A bomba de circulação também é uma alternativa desde que seja de material apropriado e permita um grande fluxo da solução.
O encanamento externo com uma bomba de circulação também mantém a solução em movimento, mas isso requer a operação de uma bomba adicional. O sistema de encanamento do tanque de dissolução precisa ser composto de tubos de polipropileno para suportar a exposição à solução extremamente cáustica.
As válvulas também devem ser de polipropileno de alta qualidade para garantir vida longa e confiabilidade ao direcionar a solução para o tanque de zincagem. O diâmetro do tubo dependerá do tamanho do tanque de revestimento e do volume de serviço que será normalmente processado. Especifique bombas que trabalhem com soluções viscosas e fortemente alcalinas sem problemas.
O número de bombas a serem utilizadas dependerá da configuração do encanamento, do tamanho da bomba e da distância que a solução precisa percorrer. Bombas e filtros devem ser dimensionados, permitindo que o volume total do banho circule de duas a três vezes por hora. Por exemplo, um banho de 5.000 litros necessita de um conjunto de bomba e filtro que permita a circulação de 10.000 a 15.000 litros/hora para um ótimo desempenho.
Filtro e bomba podem ser fornecidos separadamente ou como unidade combinada. As unidades combinadas costumam ser bem eficientes e incluem bomba, filtro, tubulação e tanque de contenção. Combinando a potência da bomba (ex.1, 3, ou 5 hp) com o correto tamanho de filtro se otimizará o fluxo da solução através da área máxima filtrante. Uma regra prática de vasão são, aproximadamente, 4.000 litros/hora para cada 10 dm2 de área filtrante.
Os filtros são imperativos para qualquer sistema de zinco alcalino e devem ser colocados anteriores à entrada do tanque de deposição (consulte as figuras 1e 2). A vida útil do filtro pode ser estendida com auxiliares de filtração, como terra de diatomáceas ou carvão ativo.
Ao usar um tanque de dissolução acoplado à bomba filtro, os elementos de filtração serão facilmente impregnados, isto prolongará o tempo para manutenção do filtro e também aumentará o poder de filtração.
Gerador de Zinco: composição, operação e manutenção da solução
Após o projeto e a instalação da linha de revestimento de zinco ter sido concluída – assim como o foram o tanque de dissolução, as bombas, filtros e tubulações –, é hora, então, de abastecer o tanque vazio com bolas/placas de zinco e solução de hidróxido de sódio. A variação da área de zinco, e a variação da concentração de hidróxido, provocarão diferentes taxas de dissolução de zinco. A operação inicial do tanque de dissolução deve ser com os cestos cheios de ½ a ¾ de sua capacidade, com solução de soda cáustica com concentração de 120 a 140 g/l.
Se ocorrer excesso de zinco na solução, simplesmente, tire uma parte do zinco dos cestos. No caso contrário, havendo pouca formação de zinco para a necessidade da linha, coloque mais zinco nos cestos (placas, bolas ou lingotes), aumentando a sua área, ou aumente a concentração de soda para 160 g/l.
O tanque de dissolução de zinco não deve apenas gerar zinco para repor o consumo eletrodepositado, ele pode também dissolver o zinco para uma nova montagem do banho em sua totalidade. Dissolvendo o zinco em múltiplas bateladas no tanque de dissolução, e transferindo essa solução para o tanque de deposição, é possível gerar milhares de litros de banho novo, pronto para uso, de zinco alcalino isento de cianetos – bastando apenas adicionar os aditivos do processo para começar a trabalhar.
Fórmulas para operar com tanques de dissolução são boas na teoria, mas em uma linha de produção, não consideram o arraste da solução, volume de produção e vários outros fatores.
O melhor é que cada linha tenha a experiência com seu tanque de dissolução de aproximadamente duas semanas, e se adapte ao seu uso de acordo com as suas características de processo, observando como o zinco deve ser gerado para manter níveis constantes de concentração de metal na solução do banho de eletrodeposição. Em geral, mantenha a solução de zinco no gerador com aproximadamente de 2 a 6 g/l acima do nível desejado no tanque de trabalho e o hidróxido de sódio, também, com concentração de 6 a 20 g/l mais alta do que a solução de eletrodeposição. Isso deve permitir que a maioria das plantas de produção consigam gerar solução de zincato em quantidade e concentração suficientes para repor o zinco na solução de deposição.
A manutenção do tanque de dissolução é bastante simples, manter o zinco nos cestos e chapas, e o hidróxido de sódio na concentração indicada, além de uma boa agitação na solução em todo o tanque do gerador, minimizarão os problemas.
Projeto de ânodos insolúveis de aço carbono
Os ânodos inertes são construídos em aço carbono ou ferro, em chapa estendida que é muito utilizada em pisos elevados/passarelas de equipamentos. A área do ânodo deve ser maximizada para permitir a distribuição adequada da placa. Existem basicamente duas maneiras de conectar os ânodos de aço aos barramentos de cobre. O método tradicional utiliza barras de cobre ou aço posicionados sobre a solução de eletrodeposição. Os ânodos de aço ficam pendurados na barra anódica.
O contato entre o ânodo e a barra anódica deve ser limpo periodicamente para impedir que óxidos formados impeçam a passagem de corrente. Precisa ser tomado cuidado quando for feita a limpeza das barras, para impedir contato do cobre com a solução de deposição. Outro método, que é o preferido, utiliza barras anódicas de aço carbono submersos na solução de deposição. Nesse caso, os ânodos podem ficar encaixados ou parafusados na barra submersa. Esse método garante contato adequado entre o ânodo de aço e o barramento, eliminando qualquer acúmulo de óxido ou isolamento nos locais de conexão. Como a corrente aplicada sai tipicamente da parte inferior dos ânodos, é benéfico escalonar a altura (profundidade) desses ânodos em todo o tanque de tratamento. Variando a extensão dos ânodos de ½ a ¾ da distância até o fundo, a corrente fluirá para diferentes áreas de trabalho, deixando mais homogênea a densidade de corrente.
Conclusão
Como o revestimento alcalino de zinco sem cianeto continua a crescer em popularidade, seria prudente a qualquer zincagem que utilize um sistema alcalino isento de cianetos considerar a instalação de um tanque de dissolução. Ânodos de zinco tradicionais requerem cuidados constantes com monitoramento e trabalho físico, o que é difícil e não prático. Embora seja possível trabalhar com os ânodos de zinco no tanque de eletrodeposição, um tanque que gere a solução de zincato eliminará muitos problemas associados aos eletrólitos de zinco alcalino isentos de cianetos.
O tanque de dissolução dá ao zincador mais controle, reduz o trabalho manual e mantém a química do banho mais uniforme por um período de tempo maior. Quando os componentes do banho estão sob controle os aditivos vão trabalhar de forma mais previsível e produzirão com mais consistência e mais qualidade a partir da linha de zincagem. Um tanque de dissolução de zinco bem projetado se comprova como grande aliado a quem opera com processo de zinco isento de cianetos.